Volume 1 - Year 2015 - Pages 11-15
DOI: TBA
Morphological Character and Floatability of Blasted Talc Particles
Onur Güven, Fırat Karakaş, Gökhan Yaşar, Mehmet S. Çelik
Istanbul Technical University
Faculty of Mines, Mineral Processing Engineering Department, Istanbul, Turkey
oguven@itu.edu.tr
Abstract - In this study, blasting method was applied to modify the morphology of particles. The extent of blasting was changed at different nozzle pressures through which shape factor and roughness of particles and their corresponding flotation recoveries were investigated. The performance of un-blasted and blasted particles in the system was measured by floating the particles of different characters in a micro-flotation cell. The results of these tests were correlated with shape factors and roughness values of particles that were analysed with Image Analysis, SEM and Optical Profilometer methods. It is shown that particles of higher angularity and roughness exhibited better floatability.
Keywords: Morphology, Blasting, Micro-Flotation, Recovery, Roughness.
© Copyright 2015 Authors - This is an Open Access article published under the Creative Commons Attribution License terms. Unrestricted use, distribution, and reproduction in any medium are permitted, provided the original work is properly cited.
Date Received: 2015-08-24
Date Accepted: 2015-11-23
Date Published: 2015-12-14
1. Introduction
In recent years, most of the investigations on flotation processes have been devoted to particle morphology and its related effects on flotation recovery [1-6]. Of these, shape factors and roughness parameters have become prominent where various hypotheses were developed and some of them were experimentally proven. The literature data relevant to this subject generally questions the influence of grinding on the characteristics of particles and variations on morphology in terms of roundness, elongation ratio, angularity, relative width and roughness which are mainly linked with the grinding conditions [7], [8]. When considered, the effect of these conditions were also studied particularly for talc particles (7] and suggesting the importance of morphological on flotation recoveries. Towards this aim, as described in a recent publication (9) basic dimensional parameters like length, breadth, width and the ratios between these units were measured and used for calculation of shape factors [10], [11], [12]. As mentioned above, to emphasize the significance of grinding and its influences on particle morphology, a plethora of research have been conducted which made it possible to develop an understanding of different forces like impact, breakup and jamming during these processes. However, apart from grinding and any kind of size reduction processes, several methods are also available for obtaining particles of different morphological properties like sand blasting, abrasion, etching [9], [19].
Of these, sand blasting treatment is generally applied to forcibly propel a stream of abrasive material against a surface under high pressure to roughen a surface with abrasive particles. This method is used for surface strengthening, cleaning and rust removal from surfaces [13], [14]. Thus, based on our knowledge about blasting and particle morphology, the effect of blasting parameters on particles except from target surfaces have not been extensively studied and evaluated in the flotation literature for talc mineral.
Thus in this contribution, the morphology of talc particles upon blasting is systematically investigated as a function of nozzle pressure. In addition, the variation of morphology of talc particles on flotation recoveries is correlatively discussed in the light of experimental data.
2. Materials and Methods
2. 1. Sample Preparation
The talc sample from Niğde (Turkey) used in experimental studies was analysed by X-Ray Fluorescence (XRF) analysis. The composition of 61.12 % SiO2, 32.40 % MgO indicated that the sample was pure enough to examine the changes in morphological properties and interpret flotation recoveries after blasting process.
The sample was first crushed by a jaw crusher to obtain particles below 1 mm in size for the blasting experiments. The crushed material (hereafter un-blasted) was then screened for 30 minutes with Fritch Ro-TAP sieve and particles of -150+106 microns in size were separated for shape factor, roughness and micro-flotation studies.
For blasting experiments, a series of tests were adopted with the uniquely designed sand blasting machine (Figure 1) as described in our previous publications [9], [19]. Hence, 100 g of un-blasted sample was fed to the blasting machine with an air stream fan across a high Mn-Stainless steel plate where the outer diameter of nozzle (d) used was 2 cm. the diameter of the point of blasting was 4 mm. The feed speed and the distance between plate and nozzle (L) were taken constant as (0.94 g/s) and 14 cm, respectively.
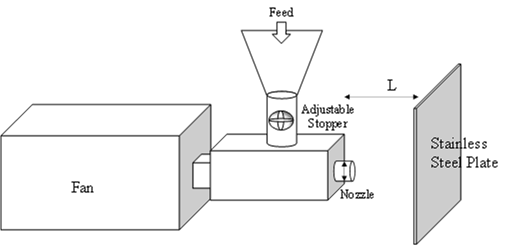
After sand blasting, the same screening procedure was applied on the blasted sample to obtain -150+106-micron size range for micro-flotation experiments and shape factor analysis.
2. 2. Sample Characterization by Image Analysis
The shape factors of both un-blasted and blasted samples were analysed using Leica QWin Image Analyze Program [15] based on the particle projections obtained from the photographs. The roundness (Ro) and angularity (A) values of about 90 particles were automatically calculated by the image analysis software by utilizing the equations defined as follows (16]:
Where “P” is perimeter, “A” is the area of particles. In addition to the shape factors, the roughness parameter for both un-blasted and blasted samples was analysed by using ZYGO New View 7100 Model optical profilometer. In this method, the measurement of height variations in non-contact mode is mainly carried out using the wave properties of light to compare the optical difference between sample surface and a reference surface. In addition, both un-blasted and blasted samples were analysed using QUANTA FEG250 Scanning Electron Microscope (SEM) at magnifications higher than 1500X in order to detect the morphological changes on the surfaces.
2. 3. Micro-flotation Experiments
Micro-flotation tests were performed using a 150 cm3 micro-flotation column cell (25×220 mm) with a ceramic frit (pore size of 15 μm) which was mounted on a magnetic stirrer and a magnetic bar used for agitation [17]. The tests were conducted at natural pH value of 7.3 with 1 g of talc sample (both un-blasted and blasted). After conditioning for 10 min, the samples were floated for 1 min using N2 gas at a flow rate of 50 cm3/min. considering the hydrophobic property of talc, only a commercial frother (MIBC) was used in order to enhance and stabilize the froth characteristics. Following 10 minutes conditioning time performed for stable dispersion in suspension, an additional 1 min conditioning time for frother was applied before starting the flotation tests. The flotation tests were evaluated by weighing the amount of particles in both float and sink products. It is worth to mention that all experiments were repeated at least three times and the average recovery for each series was presented.
Results and Discussion
3. 1. Micro-flotation Experiments with the Blasted and Un-blasted Talc Particles
Many papers in the literature have been dedicated to the effect of morphological parameters in particular those on talc flotation [2], [18]. Most of these studies have been dwelled on the influence of only grinding conditions and shape factors on natural hydrophobicity. In this study, apart from the flotation systems as column or conventional, the effect of different shape factors occurred after blasting and their effect on flotation recovery was studied by performing micro-flotation tests as a function of nozzle pressure.
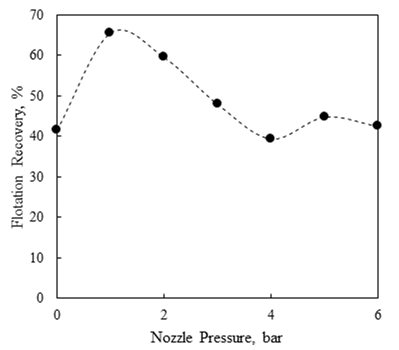
As seen from Figure 2, the recovery of about 41 % was obtained with the un-blasted sample. Besides, blasting the sample at 1 bar nozzle pressure increased the recovery up to 68 %, and then decreased it gradually down to 42% at 6 bars. Considering the same conditions for all tests and regarding the hydrophobic property of talc mineral, one possible explanation for this difference on flotation recoveries may be the changes on morphological properties especially roundness which will be discussed detailed in further section. On the other hand, a similar trend was obtained in our previous studies with the same method for quartz and glass bead particles [9], [19]. However, it is worth to note that most likely due to the structural differences of particles, maximum flotation recoveries shifted after blasting at different nozzle pressures.
3. 2. Correlation of Particle Morphology and Flotation Recoveries
Image Analysis (hereafter IA), SEM and profilometer analyses were used to analyse the effect of nozzle pressure on the particle morphology of samples and correlated with the flotation recoveries. The results of profilometer measurements such as RMS (Root Mean Square Roughness) and Ra (Average Roughness) are presented in Table 1 along with the SEM images of the samples given in Figure 3.
Table 1. Shape factors and roughness coefficients for both un-blasted and blasted talc particles.
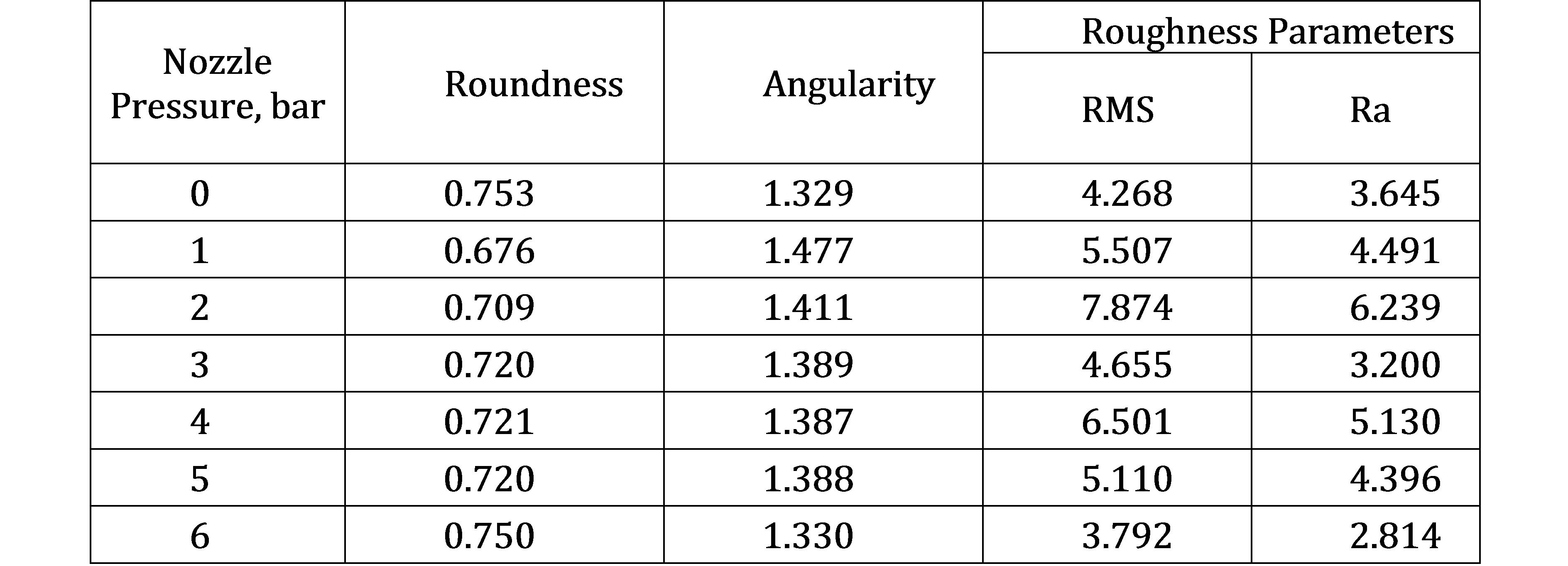
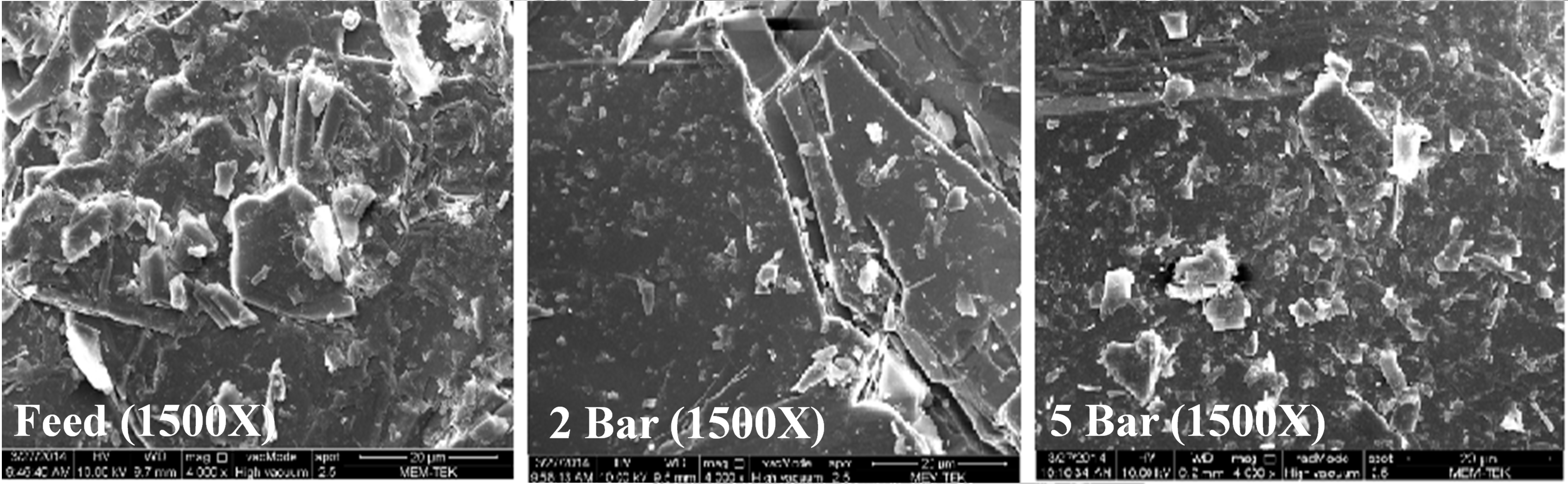
The results in Table 1 shows that the structure of talc mineral becomes more angular upon increasing the pressure up to only 1 bar above which it progressively became rounder. These characteristics of material can be explained by means of the amount of material pass through the nozzle and hit the plate. When considered, for higher nozzle pressure values, an increase on the amount of material for the same time interval resulted in fewer amounts of material getting contact with the plate. From this point of view, as the particles get in contact with plate becomes angular, the rest of the particles were kept relatively the same about their morphological characteristics, which then increase the cumulative roundness degree of materials. This in turn caused decreases in flotation recoveries. As mentioned above similar trends were also obtained for quartz where 2 bars nozzle pressure was found as the optimum value for obtaining angular particles [19]. In addition, considering soft and easily dispersible structure of talc mineral, the amount of fine material in the product of blasted material might have increased its proportion at higher pressures. Therefore, in order to prevent the effect of fine material during flotation tests, all the blasted materials were dry screened after each blasting test in order to obtain the same particle size range as -150+106 µm for flotation tests. Thus the same testing procedure was applied for quartz and glass beads in our previous tests [9], [19]. In spite of screening the particles, the presence of very fine particles may still lead to the increase of residue on the particle surface which in turn may affect the smoothness of the particles.
Figure 4 illustrates the correlation between angularity values presented in Table 1 and flotation recoveries. As it can be clearly seen from Figure 4, there is a strong correlation between angularity and flotation recoveries which is in line with the results reported in the literature [4], [6], [18], [20].
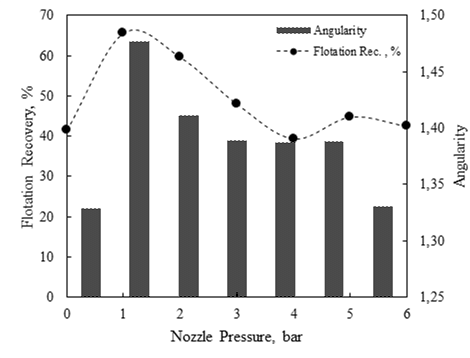
Most studies in the literature have dwelled on the effect of grinding conditions related to shape factors where relatively angular particles were produced in rod mills in comparison to other grinding systems. In this manner, Hicyilmaz et al. [8] investigated the effects of shape properties on the wettability based separation processes for ground talc particles. They found that the maximum flotation recovery of 65 % can be obtained with the feed material presenting 1.090 angularity value after grinding in a rod mill. In addition, it was also shown that significant differences between flotation recoveries could be efficiently obtained by relatively small differences on shape factors as 0.014 for roundness values which in turn gives the maximum and minimum points for flotation recoveries. Beside other flotation parameters, these results can be well ascribed to the degree of particle-bubble interaction, in other words increasing the collision probability resulted in higher flotation recoveries for angular particles. Accordingly, in a recent publication [6], this phenomenon was extensively discussed and experimentally proven by the induction time measurements with borosilicate particles having different shape factors. In short, they suggested that the induction time for attachment was significantly reduced in the case of angular particles. Under the same conditions, another publication of the same research team also showed that in contrast to the well-known hypothesis of constant induction period for a given particle and air bubble may change upon the particle’s approach trajectory to the bubble [21].
On the other hand, the trend between average roughness values and flotation recoveries was not linear as obtained for shape factors (see Figure 5). Although these results are in accordance with the previous findings in literature [2], our previous results for quartz and glass beads indicated that any increase on roughness values after blasting resulted in higher flotation recoveries which also well correlated with the shape factors.
One possible explanation for this kind of results can be the structural differences between minerals during the blasting process where talc particles may be affected less than other samples due to their laminar structure.
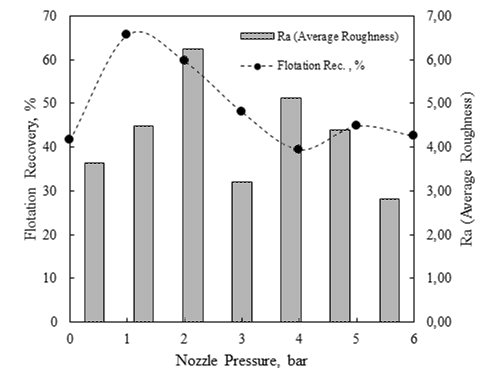
4. Conclusions
Sand blasting as an alternative approach to grinding conditions was developed for changing the morphological properties of minerals in terms of roughness and shape factors. In addition, micro-flotation experiments were conducted for blasted samples under different nozzle pressures and the results compared with un-blasted particles. The results of different analysis methods as IA, SEM and Profilometer evidently suggested that increasing the nozzle pressure up to 1 bar resulted in more angular particles and consequently higher flotation recoveries in agreement with the previously reported literature on rod mill grinding [2].
Acknowledgement
The authors extend their thanks to the The Scientific and Technological Research Council of Turkey (TUBITAK) with a project number 214M433 for the support provided.
References
[1] U. Ulusoy, M. Yekeler and C. Hiçyılmaz, "Determination of the shape, morphological and their wettability properties of quartz and their correlations," Minerals Engineering, vol. 16, no. 10, pp. 951-964, 2003. View Article
[2] H. Kursun and U. Ulusoy, "Influence of Shape Characteristics of Talc Mineral on the Column Flotation Behavior," International Journal of Mineral Processing, vol. 78, no. 4, pp. 262-268, 2006. View Article
[3] P. T. L. Koh, F. P. Hao, L. K. Smith, T. T. Chau and W. J. Bruckard, "The effect of particle shape and hydrophobicity in flotation," International Journal of Mineral Processing, vol. 93, no. 2, pp. 128-134, 2009. View Article
[4] B. Rezai, M. Rahimi, M. Aslani, A. Eslamian and F. Dehghani, "Relationship between surface roughness of minerals and their flotation kinetics," in Proceedings of the XI International Seminar on Mineral Processing Technology, India, 2010. View Article
[5] D. I. Verrelli, P. T. L. Koh and A. V. Nguyen, "Particle-bubble interaction and attachment in flotation," Chemical Engineering Science, vol. 66, no. 23, pp. 5910-5921, 2011. View Article
[6] D. I. Verrelli, W. J. Bruckard, P. T. L. Koh, M. P. Schwarz and B. Follink, "Particle shape effects in flotation. Part 1: Microscale experimental observations," Minerals Engineering, vol. 58, pp. 80-89, 2014. View Article
[7] M. Yekeler, U. Ulusoy and C. Hicyilmaz, "Effect of particle shape and roughness of talc mineral ground by different mills on the wettability and floatability," Powder Technology, vol. 140, no. 1-2, pp. 68-78, 2004. View Article
[8] C. Hiçyılmaz, U. Ulusoy and M. Yekeler, "Effects of the shape properties of talc and quartz particles on the wettability based separation processes," Applied Surface Science, vol. 233, no. 1-4, pp. 204-212, 2004. View Article
[9] O. Guven, O. Ozdemir, I. Karaagaclioglu and M. Celik, "Contribution of surface roughness on flotation of glass beads, XVII," in CD Proceedings of International Mineral Processing Congress, Chile, 2014. View Article
[10] N. Sarkar and B. Chaudhuri, "An efficient differential box counting approach to compute fractal dimension of image," IEEE Transactions on Systems, Man. And Cybernetics, vol. 24, no. 1, pp. 115-120, 1994. View Article
[11] T. Meloy and M. Williams, "Particle shape characterization, new and old methods: Does a particle have shape," Challenges in Mineral Processing, pp. 207-221, 1994.
[12] P. Singh and P. Ramakrishnan, "Powder characterization by particle shape assessment," KONA Powder and Particle Journal, vol. 14, pp. 16-30, 1996. View Article
[13] L. Guoying, Surface Engineering, Beijing: Mechanical Industry Publishing House, 1998.
[14] B. Djurovic and E. Jean, "Coating removal from fiber composites and aluminium using starch media blasting," Wear, vol. 224, no. 1, pp. 22-37, 1999. View Article
[15] LQiU Manual, "Leica Q500MC QWin User Manual," Leica Microsystems Imaging Solutions Ltd, UK, 1995.
[16] E. Forssberg and H. Zhai, "Shape and surface properties of particles liberated by autogenous grinding," Scandinavian Journal of Metallurgy, vol. 14, no. 1, pp. 25-32, 1985. View Article
[17] M. Hancer and M. S. Celik, "Flotation mechanisms of boron minerals," Separation Science and Technology, vol. 28, no. 9, pp. 1703-1714, 1993. View Article
[18] U. Ulusoy and I. Kursun, "Comparison of different 2D Image Analysis measurement techniques for the shape of talc particles produced by different media milling," Minerals Engineering, vol. 24, no. 2, pp. 91-97, 2011. View Article
[19] O. Guven, O. Ozdemir, I. E. Karaagaclioglu and M. S. Celik, "Surface morphologies and floatability of sand-blasted quartz particles," Minerals Engineering, vol. 70, pp. 1-7, 2015. View Article
[20] L. O. Filippov, R. Joussemet, M. Irannajad, R. Houot and A. Thomas, "An approach of the whiteness quantification of crushed and floated talc concentrate," Powder Technology, vol. 105, no. 1-3, pp. 106-112, 1999. View Article
[21] D. Verrelli, P. Koh, W. Bruckard and M. Schwarz, "Variations in the induction period for particle–bubble attachment," Miner. Eng., vol. 36–38, pp. 219-230, 2012. View Article