Volume 2 - Year 2016 - Pages 20-23
DOI: TBA
Mineral Processing Analysis in Artisanal Gold Mining, Peru
Hernán Anticoi, Pura Alfonso, Marc Bascompta, Sílvia Palacios
Universitat Politècnica de Catalunya, Departament d'Enginyeria
Minera i Recursos Naturals,
Av. Bases de Manresa 61-73 Manresa, Spain
hernan@emrn.upc.edu; pura@emrn.upc.edu; marc.bascompta@emrn.upc.edu; silviaminera@gmail.com
Abstract - The usage of inefficient techniques in artisanal gold mining is quite common, either to extract the ore or processing it, and always related to environmental contamination. This paper analyse the mineral processing of a case study in Peru (San Cristobal) with the aim to improve the gold recovery process and mitigate the environmental impact. The process of amalgamation (gold-mercury) has been found as ineffective due to the presence of arsenic, while the particle size is not optimal to recover the gold. Therefore, the processing equipment should be changed to improve the grade recovery. The mineral liberation and particle size distribution analysis are the key to evaluate the performance of the process.
Keywords: Gold recovering, Artisanal mining, Pollution, Mineral processing.
© Copyright 2016 Authors This is an Open Access article published under the Creative Commons Attribution License terms. Unrestricted use, distribution, and reproduction in any medium are permitted, provided the original work is properly cited.
Date Received: 2015-10-29
Date Accepted: 2016-03-24
Date Published: 2016-10-18
1. Introduction
There are between 10 and 15 million artisanal miners, mainly in Africa and Latin America, which extract an average of 350 tons of gold per year [1]. Artisanal gold mining (ASGM) is widespread in Peru, where the activity is developed without any geological and technical knowledge and the miners usually take advantage of the mining sites abandoned by large companies.
This type of mining often uses amalgamation with mercury o cyanidation to recover the gold. These gold recovering methods are cheaper than other alternatives methods and very easy to apply [2]. Nevertheless, they can result in inefficient procedures due to low degree of gold recovering. Furthermore, these products are very damaging for the health of miners, surrounding inhabitants and the environment. In addition, the tailings generated during the gold processing are not adequately controlled and subsequently the population is exposed to high levels of pollutants [3] and [4].
The aim of this work is to assess the techniques used in the San Cristobal artisanal mining site (southern Peru) to process gold and identify the weaknesses of this process in terms of production efficiency and environmental pollution.
San Cristobal is a mining settlement of about 800 inhabitants located at 3600 m of altitude. They use mercury and cyanide for gold recovering and the tailings are abandoned with still an important amount of gold and other metals.
2. Methodology
2.1. Analytical techniques
Several samples in different mineral processing stages were obtained. Besides, representative samples from the geological formation, where the mine is located, were also taken.
Chemical analyses were performed at the Activation laboratories (Actlabs), Canada, using FA-GRA and AR-ICP techniques in order to obtain faithful mineral grade. Particle size analyses were obtained in the sieve laboratory of the Department of Stratigraphy, Paleontology and Marine Geosciences at the University of Barcelona, using a Coulter Electronics LS230. For the mineralogical and textural observations, polished sections were observed on a petrographic reflected light microscope and in electron microscopy (SEM) using a Tabletop Microscope Hitachi TM-1000 equipped with an X ray Energy dispersive system (EDS) from the Polytechnic University of Catalonia and a SEM JSM-840 from the Centres Científics i tecnològics of the University of Barcelona.
2.2. Theoretical fundamentals
To separate the ore from the gangue, materials must be fragmented to obtain a grain size smaller than the size of the ore mineral.
The Wigel [5] and Gaudin [6] approaches have been applied to determine the particle liberation size using eqs. 1 to 4. As there is little data related to the mineral processing and the geology of the deposit, it is considered that the method chosen match with what is demanded in the case study.



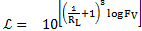


Where is
the particle liberation (%),
is the grain diameter before
fracture,
denotes
the particle diameter after comminution,
is the volumetric fraction of the ore
and
is the comminution ratio.
In a binary system composed of two minerals, A and B, the volumetric fraction and the ore grade is determined by Eq. 5.
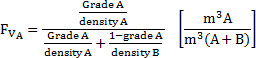
Meanwhile, Gupta [7] detailed the third comminution law, which is showed in Eq. 6.
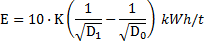
Where
W is the specific energy for grinding, and
are the particle diameters before and
after comminution and
is
the Bond ball work index, which depends on the ore response to milling. For
this case, a value of 16.31 kWhr/t was used [7][8].
3. Results and Discussion
3.1. Ore mineralogy
Ore mineralization in the San Cristobal deposit occurs in quartz veins, which are up to 1 meter wide, hosted in granitic rocks. Ore minerals are mainly pyrite, chalcopyrite, arsenopyrite, sphalerite, galena, native bismuth, sulfosalts, electrum (Au-Ag amalgam) and native gold. Malachite, azurite and calcanthite are widespread as alterations of chalcopyrite.
Native gold always appears encapsulated in the pyrite matrix, while electrum is placed within the mineral fractures. In most cases, gold and electrum particles size ranges between 8 and 10 µm, although they can reach up to 50 µm (Figure 1).
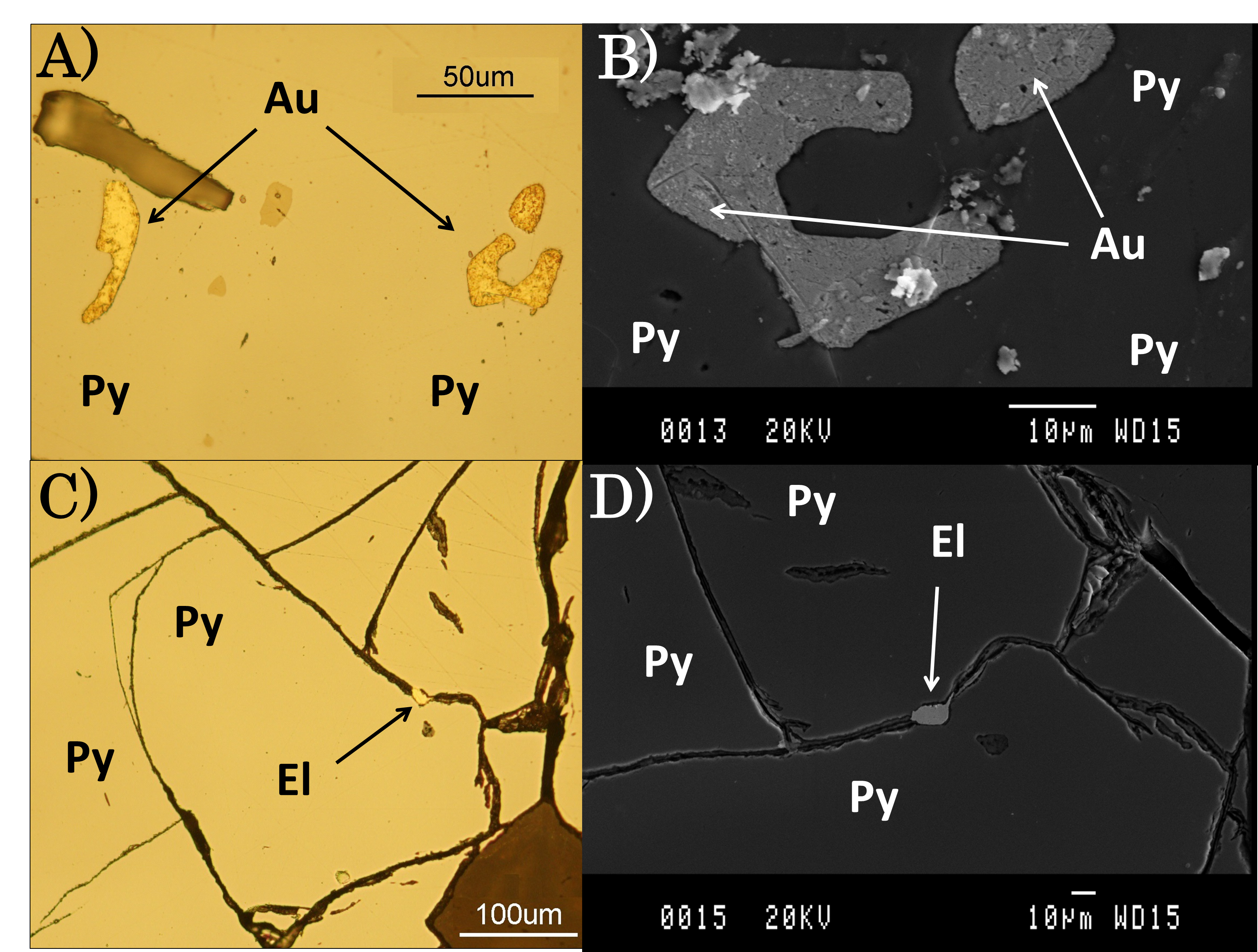
3.2. Mineral processing
The gold-bearing mineral is treated using two different comminution devices. First, it is introduced into a ball mill, where the grain size is substantially reduced from several centimetres to a few microns. Afterwards, the powder generated goes to a secondary milling stage, using an artisanal mill, that consist in a mortar with a grinding stone made of granite. Here, the powder is mixed with mercury to produce an Au-Hg amalgam. Later on, the amalgam produced is manually released from the mixture by density difference. Then, this amalgam is burnt in open vessels or in a retort to separate gold from mercury. This system allows obtaining a certain proportion of the gold enclosed in the mineral. Only the completely liberated particle can be amalgamated with mercury. Thus, the part dumped still has an important quantity of gold and other elements like silver or copper. Therefore, cyanide is applied to the tails to dissolve these elements and recover some of it by adsorption using activated carbon.
The grain size analysis of the ore after the secondary stage of milling indicates that D80 represents particles up to 160 µm, while D35 represents particles up to 20 µm (Figure 2). The calculations of particle liberation point out that the ideal diameter for a D80 particle is 0.1 µm (Table 1). In terms of energy use, the power obtained by the grinding devices is approximately 130 kWh/t and the liberation of gold particles needs 458 kWh/t.
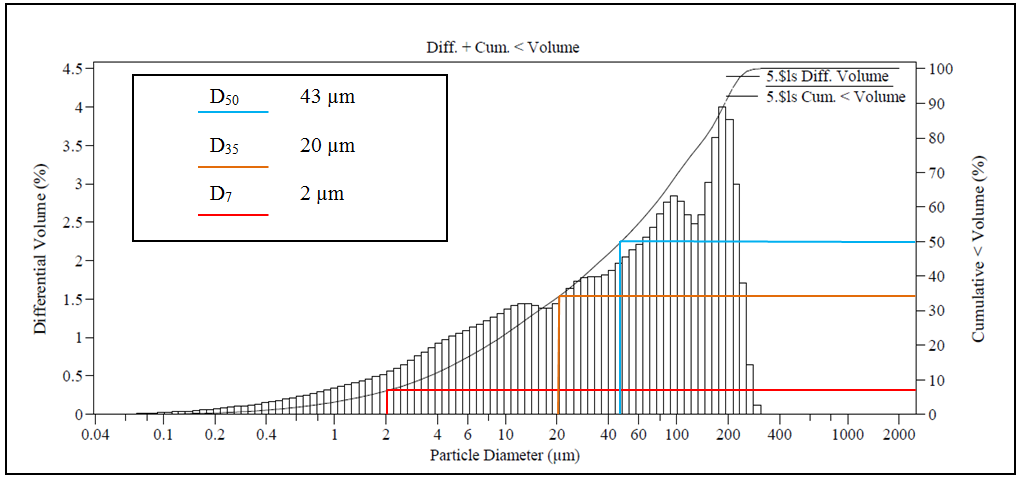
Table 1. Mineral liberation calculation for gold encapsulated in a pyrite matrix.
Particle size (μm) | Liberated (%) |
9 | 0.1 |
8 | 0.8 |
7 | 2.7 |
6 | 6.4 |
5 | 12.5 |
4 | 21.6 |
3 | 34.3 |
2 | 51.2 |
1 | 72.9 |
0.9 | 75.36 |
0.6 | 83.06 |
0.5 | 85.74 |
0.1 | 97.03 |
3.3. Chemistry of materials
The raw materials from San Cristobal deposit shows gold grades between 27 and 60 ppm Au. The gold grade is still remarkable after the amalgamation treatment, above 11 ppm (Table 2). On the other hand, the concentration after cyanidation of the tails drops considerably, between 1 and 19 ppm. In addition, the mineralization usually contains silver, between 100 to 200 ppm Ag, which is not recovered.
The high concentrations of As in the samples, due to the presence of arsenopyrite (FeAsS) in the deposit, has a negative impact in the effectiveness of Hg added in the milling stage with the idea of obtaining gold. Although mercury is found in the original mineral, its proportion increases because of the amalgamation process. Sulphide minerals may be responsible for the high consumption of mercury amalgamation process. This phenomenon is especially important when there is arsenopyrite, because arsenic has priority to react with mercury instead of gold [9]. Which Worsen the environmental effect of the mineral process.
The ore mineralization of San Cristobal is also rich in Cu, with, more than 0.1 wt. %, but this metal is not recovered.
Table 2. Representative analyses of the metal concentrations in different stages of the mineral processing in San Cristobal.
Sample | Stage | Au (ppm) | Ag (ppm) | Hg (ppm) | As (ppm) |
QU2 | Original mineral | 27.8 | 138 | 228 | 428 |
QU1 | Post-amalgamation | 11.1 | 175 | 589 | 472 |
QU3 | Post-Cyanidation | 1.33 | 57 | 6 | 291 |
SRC2 | Original mineral | 33.2 | 117 | 9 | 519 |
SRC1 | Post-Cyanidation | 18.5 | 176 | 917 | 434 |
3.4. Pollution issues analysis
Artisanal miners are exposed to pollutant during the process by two main sources:
- Direct contact with mercury to produce the amalgam.
- Breathing mercury vapour when the amalgam is burned to separate gold.
However, there are other indirect contamination sources due to the mining activity. As considerable quantities of mercury is dumped to the rivers and surrounding areas, mercury can be transformed to metyl-mercury, which is an extremely cancerogenous organic compound. Moreover its persistence in the environment and the high percentage of accumulation can prolong the polluting effect after several cycles [10].
On the other side, the risk associated with cyanidation is comparatively low, because cyanide has not persistence in the environment along the time and only a directly consumption of this element could produce damage in human health. Despite that, it has to be pointed out that a very low dose can be fatal; the lethal dosage is around of 4.7 ppm [11]. The cyanidation process does not receive any treatment to neutralize them.
4. Conclusion
- In the San Cristobal deposit native gold is encapsulated in a pyrite matrix, whereas electrum is placed within the fractures of pyrite.
- The high consumption of mercury is caused by the presence of arsenopyrite with the gold ores. It should be advisable to change the gold obtaining process by mercury to another alternative.
- The energy required to liberate the gold particles is 458 kWh/t, meanwhile the energy used is 130 kWh/t. Besides, liberation degree shows that the particle size of the product is not enough to break the pyrite matrix and liberate gold. Thus, the current equipment is clearly insufficient to work efficiently.
- The metals concentration analysis displays that cyanidation process has a higher degree of gold recovery than Hg amalgamation.
- Either cyanide or mercury should be managed with the aim to reduce their impact to the environment. Using them in a closed cycle if it is not possible to replace them for other less harmful products.
Acknowledgements
This study was partly financed by the Centre de Cooperació al desenvolupament (CCD) of the Universitat Politècnica de Catalunya. The authors would like to thank the miners from San Cristobal for their willingness and the NGO Mineria pel Desenvolupament (MpD).
References
[1] L. D. Lacerda, "Updating global Hg emissions from small-scale gold mining and assessing its environmental impacts," Environmental Geology, vol. 43, pp. 308-314, 2003. View Article
[2] H. Gibb and K. G. O'Leary, "Mercury Exposure and Health Impacts among Individuals in the Artisanal and Small-Scale Gold Mining Community: A Comprehensive Review," Environmental Health Perspectives, vol. 122, pp. 667-72, 2014. View Article
[3] P. Cordy, M. Veiga, I. Salih, S. Al-Saadi, S. Console, O. Garcia and M. Roeser, "Mercury contamination from artisanal gold mining in Antioquia, Colombia: The world's highest per capita mercury pollution," The Science of the Total Environment, pp. 154-60, 2011. View Article
[4] G. Hilson and R. van der Vorst, "Technology, managerial, and policy initiatives for improving environmental performance in small-scale gold mining industry," Environmental Management, vol. 30, no. 6, pp. 764-77, 2002. View Article
[5] R. Wigel, "Integrated size-reduction-mineral liberation model," Trans. Soc. Min. Eng. AIME, vol. 260, pp. 147-52, 1976. View Article
[6] A. Gaudin, Principles of Mineral Dressing, New York: McGraw Hill Book Co., 1939. View Article
[7] E. G. Kelly and D. J. Spottiswood, Introduction to mineral processing, Mineral Engineering Services, 1989. View Article
[8] A. Gupta, Mineral Processing Design and Operation: An Introduction, Netherlands, Elsevier, 2006. View Article
[9] H. Wotruba, "Reducing mercury emissions in small scale mining-experiences from South America," in EPD Congress; Extraction and Processing Division, San Diego, CA, United States, 2003. View Article
[10] M. Gabriel and D. Williamson, "Principal biotechnical factor affecting the speciation and transport of mercury through terrestrial environment," Publicación Periódica; Environment Geochemistry and Health, vol. 26, pp. 421-434, 2003. View Article
[11] A. Carbonell, F. Burlo and J. Mataix, Arsénico en el sistema suelo-planta. Universidad de Alicante, Spain, Gráficas Vidal Leuka, S. L., 1996. View Article