Volume 5 - Year 2019 - Pages 7-18
DOI: 10.11159/ijmmme.2019.002
Flotation of lithium ores to obtain high-grade Li2O concentrates. Are there any mineralogical limitations?
Rui Sousa1, Violeta Ramos2, Alexandra Guedes2, Ana Botelho de Sousa1, Fernando Noronha2, Mário Machado Leite1
1Laboratório Nacional de Energia e Geologia
Rua da Amieira, Apartado 1089, S. Mamede de Infesta, Portugal
rui.sousa@lneg.pt; ana.botelho@lneg.pt; machado.leite@lneg.pt
2Institute of Earth Sciences, Porto Pole; Department of Geosciences, Environment and Spatial Planning of the Faculty of Sciences of the University of Porto
Rua do Campo Alegre, 4169-007 Porto, Portugal
violetaramos@fc.up.pt; aguedes@fc.up.pt; fmnoronh@fc.up.pt
Abstract - The current lithium demand for batteries in general and namely for the electrical vehicle, awakened the attention for mineral processing of lithium ores. The largest lithium reserves are in brines from western South America and in pegmatites. Throughout Europe it is possible to identify several lithium deposits, namely in granitic pegmatites. An efficient mineral processing approach could be the key for an economically viable mining project. This work addresses a mineral processing study by froth flotation of samples collected in two European lithium ore pegmatites deposits - Länttä (Finland) and Gonçalo (Portugal) and aims at paying attention to some mineralogical features that can decrease the mineral processing efficiency and consequently the upgrading of the Li2O concentrates. In the case of Länttä, spodumene is the main lithium mineral and a grade of 5.20 % Li2O is the maximum obtained in the concentrates, whilst lepidolite is the lithium-bearing mineral in Gonçalo and that can be concentrated by froth flotation up to 4.50 % Li2O. Taking into consideration the Li2O content of both Länttä spodumene and Gonçalo lepidolite, respectively 7.0 and 5.58 % Li2O, higher concentrate grades would be expected. In both studied cases, very fine quartz and albite inclusions locked in lithium silicates were identified justifying the existence of a limitation for the processing technology. The mineral processing of the two pegmatites revealed the difficulty of producing Li2O close to the stoichiometry of the spodumene and lepidolite in either of these two ores.
Keywords: Liberation, Froth flotation, Spodumene, Lepidolite, Granitic pegmatites.
© Copyright 2019 Authors This is an Open Access article published under the Creative Commons Attribution License terms. Unrestricted use, distribution, and reproduction in any medium are permitted, provided the original work is properly cited.
Date Received: 2018-07-03
Date Accepted: 2018-10-31
Date Published: 2019-02-15
1. Introduction
Unique properties make lithium a key metal for modern life with its low density, electrochemical activation, high redox potential, and high specific heat capacity [1].
The present tendency for the development of portable devices and the application of batteries as power sources in electric cars and tools are creating an extra demand for lithium, being one of the most important strategic raw materials for many industries [2]. Batteries are considered the most suitable option for conservation, storage, and transmission of renewable energy. The capability of storing a large amount of energy within a given volume-to-mass ratio in a short period of time is considered the most critical characteristic of any battery [3, 4] and the lithium ion batteries are considered the most promising way to capture energy [5]. Due to that fact, the application of lithium ion batteries in the rechargeable batteries technology would be essential for the industrial growth, to reduce the environmental constraints linked to the traditional energy transmission technologies, to enhance the energy security, and to improve the daily life conditions [6, 7]. Lithium also finds application in other industries, such as ceramics, glass, primary aluminium production, pharmaceutical, manufacture of lubricants and greases, synthesis of vitamin A and organic compounds, among others [8, 9, 10, 11].
In 2016, the countries with the largest lithium reserves worldwide were Chile (7.5 Mt), China (3.2 Mt), Argentina (2 Mt), Australia (1.6 Mt), Brazil (0.48 Mt), Portugal (0.06 Mt), United States (0.038 Mt) and Zimbabwe (0.023 Mt). For the same considered year, the major countries in worldwide lithium mine production were Australia (14,300 t), Chile (12,000 t), Argentina (5,700 t), China (2,000 t), Zimbabwe (900 t), Portugal (200 t) and Brazil (200 t) (data in metric tons of lithium content) [12].
The main sources for lithium are brines and magmatic rocks rich in lithium silicate minerals and/or phosphates. The most important rock deposits of lithium are granitic pegmatites and greisens. It has been estimated an average lithium content on Earth’s upper continental crust of 21 ppm [13], included in more than 20 minerals. However, just some of them occur in magmatic crystalline rocks and have commercial/industrial potential – lepidolite, spodumene, petalite, amblygonite-montebrasite and zinnwaldite [2, 14].
Lithium is supplied to industry in the form of lithium carbonate, sulfate, hydroxide, chloride, bromide, and butyllithium [15]. It is crucial to determine accurate processes to obtain high-lithium grade concentrates prior to the development of new lithium-based technologies. Therefore, it is imperative to find mineral processing strategies that maximize the lithium recovery and allow for the achievement of valuable lithium-rich concentrates. Usually, the enrichment process starts with the crushing and grinding steps to attain lithium minerals liberation and, at the same time, adjusting the size of particles for the concentration processes [16, 17]. The global challenge for lithium pegmatites is to award the label of green industry when reaching the level of almost “zero waste” mining by also producing quartz and low iron feldspar. Optical sorting and heavy liquid separation could be applied as pre-concentration stages, while flotation could be applied as the final concentration step and gravity separation used to recover other secondary minerals [18, 19]. Froth flotation has become the most important and efficient method for lithium ores processing [20]. Previous studies showed the possibility of obtaining high-lithium grade concentrates by froth flotation from Portuguese ores, as are the cases of amblygonite (Argemela deposit) and spodumene (Barroso) assaying values close to the stoichiometry of the respective minerals [18, 21]. Furthermore, in neighbouring Galicia (Spain), an attempt to optimize the flotation of spodumene from Vilatuxe pegmatite, district of Pontevedra, was successfully carried out producing concentrates of about 6.5 % Li2O [22].
Under the scope of FAME (Flexible and Mobile Economic Processing Technologies) H2020 project, which focused on improving mineral processing technologies for the recovery of valuable materials from low grade European ores, the feasibility of froth flotation of lithium silicates from pegmatites to produce high-grade Li2O concentrates was investigated. For that purpose, samples from two lithium pegmatites, a spodumene-rich from Länttä (Finland) and a lepidolite-rich from Gonçalo (Portugal), were selected from the target ores considered on the FAME project. This paper reports a detailed mineralogical study as a crucial step for the interpretation of some results experimentally obtained.
2. Geology
2.1. Spodumene-rich pegmatite from Länttä (Finland)
The pegmatite deposit of Länttä, Western Finland, is located at Ullava, about 60 km southeast of Kokkola town. The Länttä pegmatite occurs in the Kaustinen lithium province that covers roughly 500 km2 in the Paleoproterozoic Pohjanmaa Schist Belt (1.92 Ga), which forms a 350 km long and 70 km wide arc-shaped belt between the Central Finland Granite Complex in the East and the Vaasa Migmatite Complex in the West (Figure 1). The pegmatites are younger than the 1.89-1.88 Ga peak of regional metamorphism, have an age of 1.79 Ga (U-Pb columbite age) and crosscut Svecofennian 1.95–1.88 Ga supracrustal rocks, which are composed of schists with some intercalations of sulphide-bearing black schists and volcanic metasediments. The metamorphic grade in the Pohjanmaa Schist Belt varies from low amphibolite facies in the eastern part to high amphibolite facies towards the Vaasa Granite complex [23]. At least, 16 separate albite-spodumene-pegmatite occurrences are known in the Kaustinen lithium province [24].
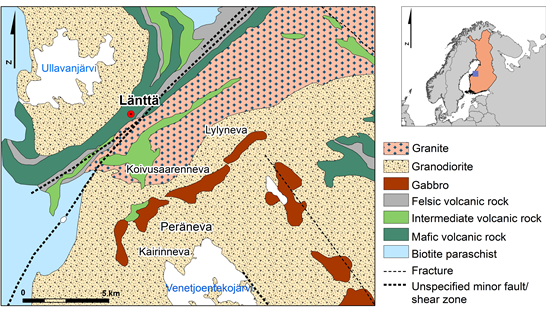
The Länttä deposit consists of two main pegmatite dikes of a maximum thickness of about 10 m together with some nearby smaller parallel dykes at the contact between meta-volcanic rocks and schists. The dykes run NW-SE, and are almost vertical or dipping 70° to SE. The thickness of the overburden in the area averages 4 m, varying between nearly 0 and 7 m.
The Länttä pegmatites can be classified as belonging to the REL-Li subclass, albite-spodumene type of the LCT (Li, Cs, Ta) pegmatite family [25] and constitute a typical example of a homogenous albite-spodumene pegmatite (56 % albite, 25 % quartz and 16 % spodumene). Columbite, cassiterite, beryl, muscovite, K-feldspar, garnet, apatite, zircon, tourmaline, lithiophilite-triphylite, topaz, gahnite spinel, calcite, pyrite, arsenopyrite, sphalerite, and bismuthinite are also present [26].
The major lithium ore is spodumene that occurs as large crystals of 4-10 cm, but can reach up to 30 cm, and is mainly light green, partly light pink or red. The total mineral resources are 1.3 Mt @ 1.08 wt% Li2O with a cut-off value at 0.50 wt% Li2O [27].
2.2. Lepidolite-rich pegmatite from Gonçalo (Portugal)
The Gonçalo pegmatite district is located in Central Portugal, approximately 20 km south of Guarda town, not far from the eastern border of Spain, and covers an area of 100 km2 of the Central Iberian Zone in the western extreme of the European Variscan Belt. The pegmatites are granitic in composition occurring as veins cutting a synorogenic Variscan coarse-grained porphyritic biotite>muscovite granite (Guarda granite) with 304.1±3.9 Ma [29] (Figure 2).
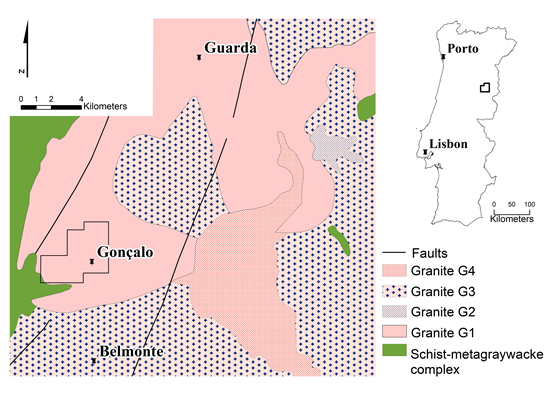
The majority of the veins run E-W to ESE-WNW slopping 20º to 30º E, up to 3.5 m thickness and corresponding to an intimate association of rocks with pegmatitic and aplitic texture that, from now on, will be referred to as pegmatite sills.
The lithium-rich pegmatite sills can be macroscopically distinguished by their typical violet colour due to the presence of lepidolite. The pegmatitic facies is characterized by lepidolite, albite, Li-muscovite, quartz, and K-feldspar as major minerals, and montebrasite, topaz, cassiterite, columbite-tantalite, beryl, petalite, and zircon as minor minerals. The aplitic facies is characterized by a sodolithic composition with lepidolite, albite, montebrasite, and quartz as major minerals; some muscovite, topaz, cassiterite, and columbite-tantalite can also occur [30, 31]. In both facies, secondary phosphates are also present, resulting from late alteration processes. Petalite is altered to kaolinite, cookeite, pollucite, and illite/smectite in late episodes of the pegmatite history.
The Gonçalo pegmatite sills exhibit mineralogical and chemical features typical of peraluminous, Li- and P-bearing Rare Element (REL) pegmatites, suggesting a model of crystallization in successive steps where concentration in fluxing agents (F, Li, P, B, etc.) was progressively enhanced to saturation with the crystallization of montebrasite and lepidolite [31]. The Gonçalo pegmatite can be classified as belonging to the REL-Li subclass, complex lepidolite type of the LCT pegmatite family [25].
Lepidolite is the most abundant lithium ore and occurs in both facies with different grain sizes. In the first case, it occurs mainly as medium to coarse-grained (> 500 µm), whereas in the aplitic unit it frequently forms fine-grained (250-60 µm) to very fine-grained (≤ 60 µm) aggregates.
Zinnwaldite is present as result of the biotite metasomatic alteration in the host coarse-grained porphyritic biotite>muscovite granite located in the contact with the pegmatite sills. As petalite and minor Li- and P-bearing minerals, such as montebrasite and zinnwaldite, are present, the lithium content in the bulk samples does not correspond only to the lithium content of lepidolite.
The inferred mineral resource estimate is of 1.5 Mt @ 1.1 % Li2O; this is a minimum value, because only lithium-rich pegmatites and a maximum quarry front of 10 m were considered for this estimation. Therefore, it is an appraisal that regards only the superficial part of the ore deposit [32].
3. Experimental
3.1. Materials and Sample Preparation
In this study samples of pegmatites from the Länttä spodumene deposit (Finland) and from the Gonçalo lepidolite deposit (Portugal) were studied. The same comminution diagram was applied to all samples to produce material with suitable size for froth flotation (Figure 3). Samples were primarily crushed in a jaw crusher (single toggle 5’’x 6’’, 4 kW, 325-375 rpm, Denver) and in a cone crusher, followed by a rod mill. Figure 4 shows the particle size distribution (PSD) of both samples after the comminution. All material is below 425 µm. It can be seen that almost 30 % of the sample mass is below 53 µm, which must be removed before flotation, since the presence of fine particles reduces flotation efficiency. Table 1 shows the main size parameters and Li2O grades of the studied samples.
Table 1. Samples grain size and grade characterization.
Sample Id | k100 (µm) | k80 (µm) | Li2O Grade (%) |
Länttä | 425 | 150 | 1.00 |
Gonçalo | 425 | 160 | 1.20 |
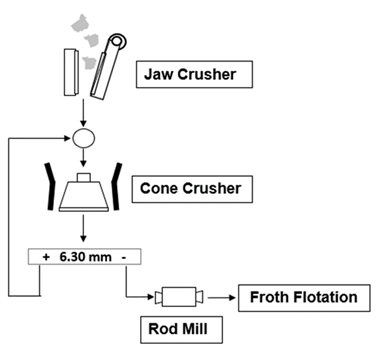
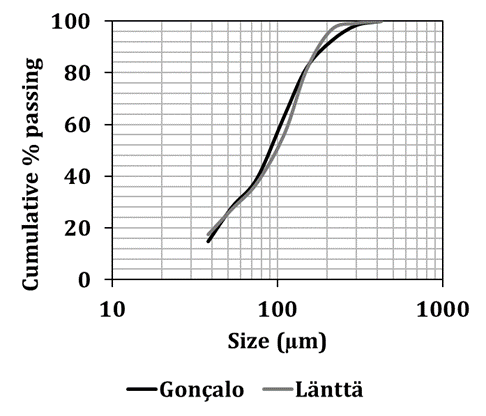
3.2. Froth Flotation tests
As mentioned before, froth flotation has become the most important and efficient method for lithium mineral processing [21], consequently it was the method applied to concentrate both lithium-rich pegmatites. Figure 5 presents the flotation flow sheet developed: a previous “desliming stage” is crucial for slimes removal, followed by three flotation stages, starting with a rougher stage. The rougher concentrate (RC) was upgraded in a cleaning stage, that produced a final clean concentrate (CC) and a middling product with high-lithium content (CT). A scavenger stage was applied to the rougher tailings (RT) to produce the final tailings (ST) and a low-lithium minerals middling product with low-lithium content (SC). Different flotation tests were carried out using distinct chemical reagents. Experimental work was conducted following reagent strategies mentioned by different authors [18, 33, 34, 35]. In the case of Länttä ore (spodumene pegmatite) tests were performed at room temperature, using two different collectors (Test A – Oleic acid; Test B – Fatty acid Aero 704 from Solvay®). An optimal pH=8.8 was maintained using NaOH. The collector was then added in two stages, at dosages of 750 g/t to the rougher and 370 g/t to the scavenger, both emulsified with fuel oil (3 kg/t). The conditioning time was 5 minutes for each stage. In the case of Gonçalo lepidolite, pH was maintained at 3 as widely referred in the literature and the collector Flotigam EDA (from Clariant®) was added at a dosage of 200 g/t in the first conditioning stage and 100 g/t in the second one, both conditioned for 3 minutes. Froth flotation tests were conducted in a Leeds open-top laboratory flotation machine with a 3.0 L cell, at an impeller speed of 1000 rpm and an air flow rate of 7.5 L/min. These reported tests were chosen among others, carried out to assess the feasibility of froth flotation to produce Li2O concentrates.
Concentrate grades are influenced by the reagent strategy. However, as flotation is a time dependent process, in the first moments of the flotation kinetics, it is usual to obtain high-grade concentrates close to the theoretical Li2O content of each mineral, because well-liberated particles of lepidolite or spodumene are the first to float. In the reported cases, high Li2O grades were never obtained, even in the beginning of the process, meaning that floated particles, although apparently well-liberated, would not be of pure lepidolite or spodumene. These cases were considered good examples for the development of a joint research between mineralogy and technology. Chemical assays of the flotation products were determined by atomic absorption spectrometry (UNICAM-M SERIES). These tests are part of an extensive experimental program, developed in the framework of FAME project, that included analysing the influence of variables such as pH, collector type and dosage, particle size distribution, pulp density and residence time.
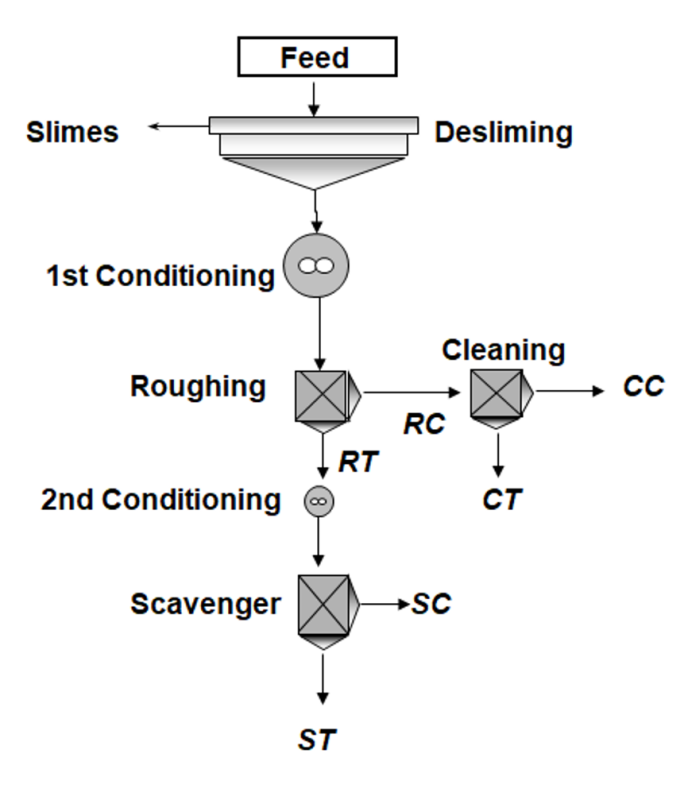
3.3. Mineralogy Assessment
The mineralogical study of samples from both pegmatites was carried out using optical microscopy, scanning electron microscopy (SEM) with energy dispersive spectroscopy (EDS) analyses and Raman microspectroscopy. Petrographic analyses of polished thin-sections were performed using a stereomicroscope Zeiss Stemi SV11 Apo coupled to a Sony Cyber-Shot DSC-S75 digital camera and also using a Leica DM LSP polarizing microscope, with transmitted and reflected light, coupled to a Leica camera with LAS EZ software 2.0.0. SEM/EDS analyses were carried out at the Materials Centre of the University of Porto (CEMUP), using a FEI Quanta 400 FEG-ESEM/EDAX Genesis X4M instrument. SEM was operated at 15 kV in high-vacuum mode, manual aperture, 4.5 µm beam spot size. Raman analyses were carried out using a Raman spectrometer Horiba Jobin-Yvon LabRam microscope XploRATM equipped with an excitation wavelength of 532 nm from an Ar laser at a power of 25 mW and with diffraction gratings with 1800 lines mm-1. A 10x objective lens of an Olympus optical microscope was used to focus the laser beam on the sample and also to collect the scattered radiation. A charged coupled device (CCD) camera was used to collect the Raman spectra. Silicon (characteristic peak at 520.5 cm-1) was used as a standard for the calibration of the equipment.
Complementary studies were carried out for the flotation concentrates by X-ray powder diffraction (XRD) using a PANALYTICAL X’PERT α-1 for the identification of the main minerals. The Rietveld Refinement method was applied to quantify the main minerals present in the concentrate.
4. Results and Discussion
4.1. Mineral Processing Experiments
4.1.1. Länttä spodumene
The results of the froth flotation tests are reported in Table 2 and Figure 6.
Table 2. Results of the froth flotation of the Länttä sample: Test A using Oleic Acid and Test B using Aero 704 as collectors (*calculated values based on mass balance). RC-Rougher Concentrate; RT-Rougher Tailings; CC-Cleaner Concentrate; CT-Cleaner Tailings; SC-Scavenger Concentrate; ST-Scavenger Tailings.
Test A - Oleic Acid | Test B - Aero 704 | |||||
Yield % | Li2O Wt.% | Recovery % | Yield % | Li2O Wt.% | Recovery % | |
CC | 7.3 | 5.2 | 35.4 | 14.5 | 3.7 | 50.2 |
CT | 12.1 | 1.6 | 18.2 | 15.8 | 1.0 | 14.1 |
SC | 12.2 | 0.9 | 35.4 | 14.5 | 3.7 | 50.2 |
ST | 68.4 | 0.6 | 36.1 | 64.2 | 0.5 | 31.4 |
RC | 19.4 | 2.9* | 53.5 | 30.3 | 2.3* | 64.3 |
RT | 80.6 | 0.6* | 46.5 | 69.7 | 0.5* | 35.7 |
Feed | 100 | 1.1* | 100 | 1.1* |
Concerning the collector comparison, it is possible to conclude that the Oleic Acid allowed for a higher concentrate grade, although at lower mineral recovery, when compared with Aero 704. It is also noted that 5.2 % Li2O is the highest grade ever obtained, result that would not be expected having in mind that the Lӓnttӓ spodumene is coarse-grained, because at flotation sizes (k80=0.150 mm) there would be a significant amount of well-liberated spodumene particles, which would have allowed to obtain concentrates with grades close to the Lӓnttӓ spodumene Li2O content (7.0 % Li2O [36]). It can be said that as the selectivity of the process is claimed (cleaning stage), it is possible to observe a better behavior of the grade-recovery curve, which means that some spodumene is already liberated, but it is not enough to produce concentrate grades above 5 % Li2O under higher metal recovery. Moreover, it is expected that the grade-recovery curve shows a prompt increase of the grade for high-recoveries, which is not the case, suggesting that spodumene is floating together with gangue minerals.
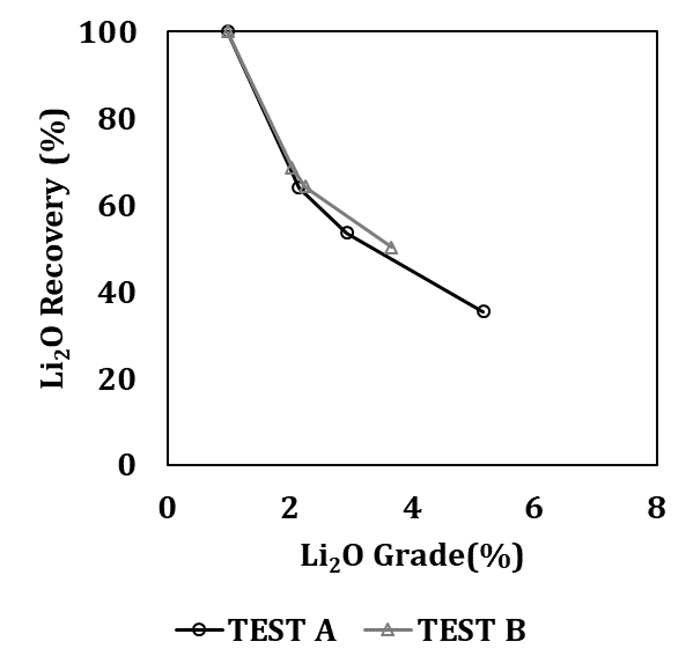
Thus, this result could be explained by the lack of mineral liberation, even if an extreme size reduction was performed.
4.1.2. Gonçalo lepidolite
Concerning the Gonçalo lepidolite, the results of the froth flotation tests are reported in Table 3 and Figure 7 shows the correspondent grade-recovery curve.
Table 3. Results of the froth flotation tests of the Gonçalo sample (*calculated values based on mass balance). RC-Rougher Concentrate; RT-Rougher Tailings; CC-Cleaner Concentrate; CT-Cleaner Tailings; SC-Scavenger Concentrate; ST-Scavenger Tailings.
Yield % | Li2O Wt.% | Recovery % | |
CC | 7.7 | 4.5 | 24.1 |
CT | 20.1 | 3.2 | 45.1 |
SC | 7.2 | 2.8 | 13.9 |
ST | 65.1 | 0.4 | 16.8 |
RC | 27.7 | 3.6* | 69.3 |
RT | 72.3 | 0.6* | 30.8 |
Feed | 100 | 1.4* |
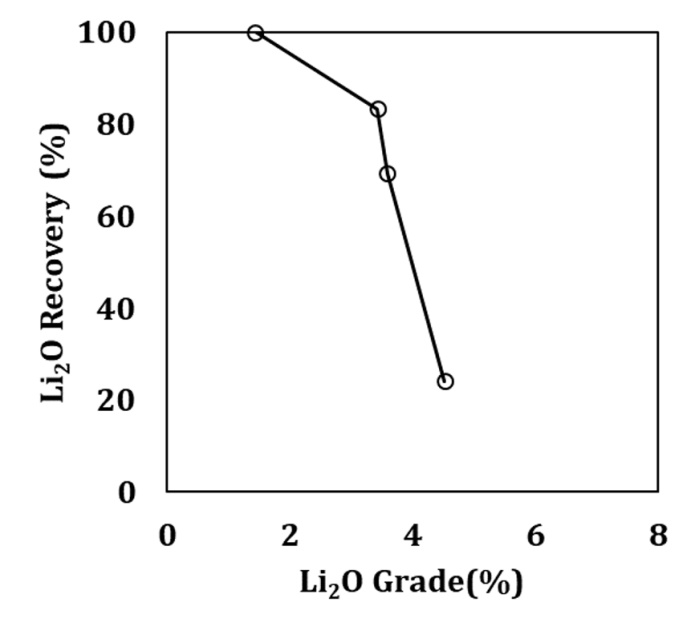
Similarly to what occurred with spodumene, it was not possible to obtain concentrates with Li2O grades close to the Gonçalo lepidolite Li2O content (5.58 % Li2O [31]), even after the cleaning stage, having been 4.50 % Li2O the maximum value achieved. The shape of the grade-recovery curve indicates that the flotation of lepidolite was more efficient than in the case of spodumene, due to the faster increase of the grade in the beginning of the flotation. However, after reaching a certain value, the concentrate grade increases only slightly, when recovery decreases. This means that during the lepidolite flotation other minerals are also floating, which could be due to the lack of lepidolite liberation, even when a significant reduction in the particle size occurred.
4.2. Mineralogy
In order to have a better understanding of the results obtained, a mineralogical study, at a detailed micrometer scale, was carried out to look for any specific textural features that could justify the processing results obtained for spodumene and lepidolite concentrates. In both cases, there were evidences of other minerals that are also floating along with the Li minerals, even after the cleaning step and working below 0.150 mm top grain size.
4.2.1. Länttä pegmatite
The mineralogy of the Länttä pegmatite was investigated by petrographic microscopy, SEM/EDS and Raman spectroscopy and it was mainly focused on the association spodumene + quartz. It was found that spodumene is intergrown with quartz. Quartz intergrowths tend to be coarser (up to 250 µm long) and graphic-shaped towards the core of the large spodumene crystals, whilst near the borders, in the contact with albite and quartz grains, quartz intergrowths tend to be reminiscent of “myrmekite” or even fibrous (Figure 8). Similar aspects were described by [37] for Neoproterozoic spodumene pegmatites from southern Natal, South Africa. In the Iberian Peninsula, some petalite-rich pegmatites exhibit a similar texture [e.g. 38] named as SQUI [39] characterized by symplectic or fibrous intergrowths of spodumene + quartz due to the breakdown of petalite. However, it must be highlighted that petalite does not occur in the Länttä pegmatite.
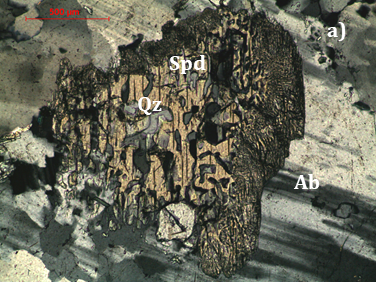
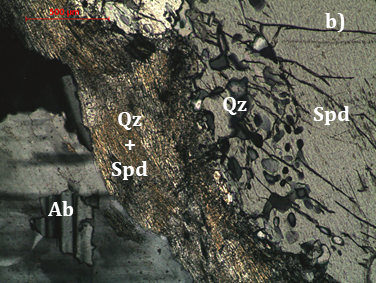
Two Raman spectra were obtained: one was performed on the core of a spodumene crystal; the other was obtained on a fibrous intergrowth at the margins of this crystal. The spectrum of the fibrous material shows the overlap of the spodumene spectrum with quartz (peak at 466 cm-1), corresponding to an intergrowth of spodumene + quartz (Figure 9).
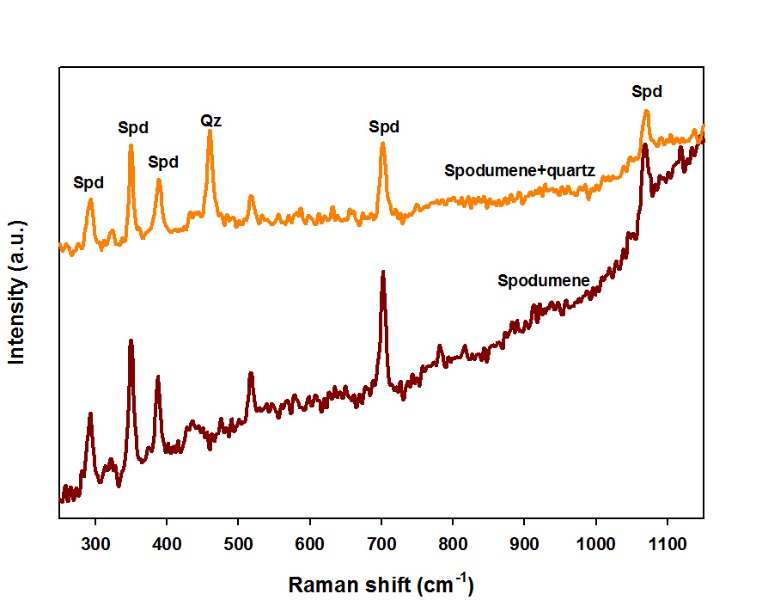
SEM analyses were also carried out. As expected, the backscattered images (BSE) show spodumene with fine quartz intergrowths, albite replacing spodumene and K-feldspar in thin veinlets (Figures 10 and 11).
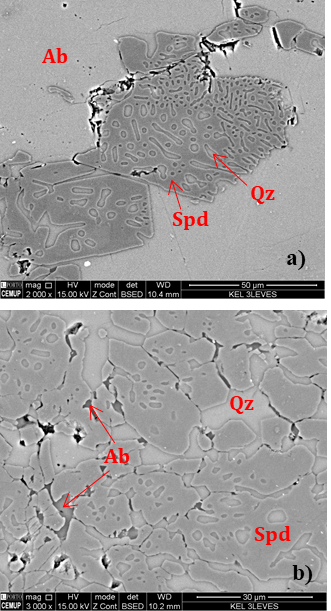
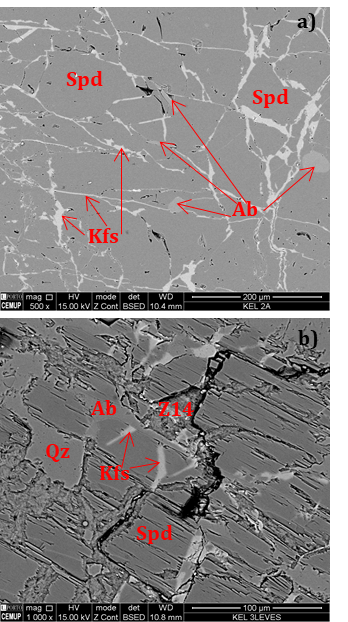
The concentrate of spodumene flotation (Test A) was analyzed by XRD indicating the existence of albite and quartz in the spodumene concentrate (Figure 12).
Applying the Rietveld Refinement, it was possible to quantify the main minerals present in the concentrate: 59.7 % spodumene, 21.9 % albite and 18.4 % quartz. However, the refinement method did not reach a good agreement of statistical criteria due to the overlapping albite and spodumene reflections and also to the inclusions of quartz in the spodumene that produce a broadening of the peak base for the most intense reflections. This broadening of the peak base is an indicator of the presence of locked particles, even at those fine sizes.

4.2.2. Gonçalo pegmatite
Petrographic studies in the case of Gonçalo revealed that lepidolite crystals frequently present microinclusions of quartz and albite as shown in Figure 13.
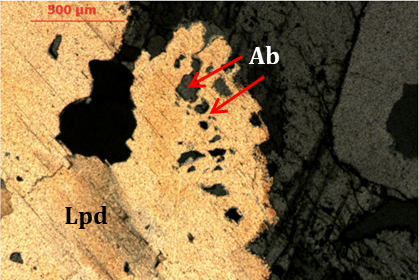
Raman analyses performed on the Gonçalo lepidolite samples (Figure 14), both from the aplitic (spectrum Lepidolite-A) and the pegmatitic facies (spectrum Lepidolite-P), show distinct Raman features: the spectrum of the pegmatitic material (coarse lepidolite) gives a typical lepidolite spectrum with well-visible peaks at 265 and 714 cm-1; in the case of the aplitic facies, the spectrum usually shows similar features to an association of lepidolite and albite (albite peaks at 297, 485 and 514 cm-1).
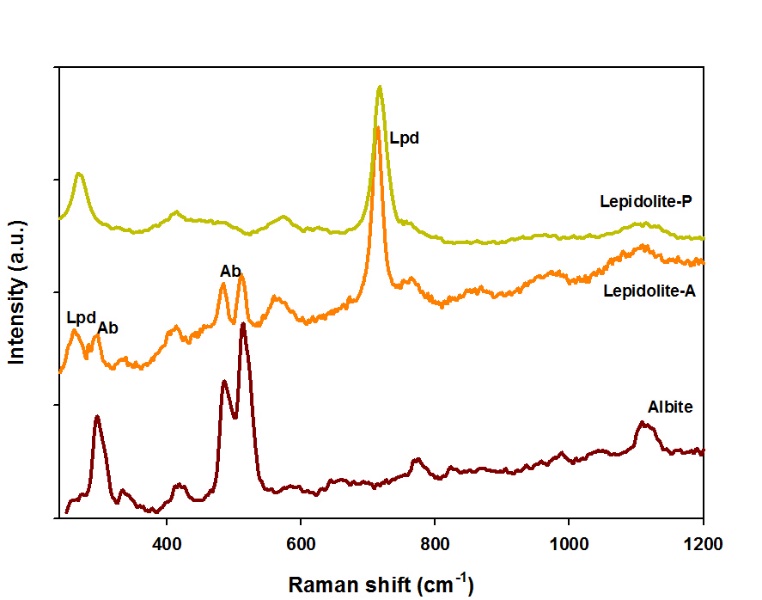
Concerning the lepidolite flotation, the XRD spectrum in Figure 15 indicates the existence of quartz and albite besides lepidolite as the major component.
Applying the Rietveld Refinement, it was possible to quantify the main minerals present in the concentrate: 19.1 % albite, 23.9 % quartz and 57.1 % lepidolite. Once again, the refinement method did not reach a good agreement of statistical criteria due to the overlapping of albite and lepidolite as well as inclusions of quartz or albite in lepidolite that produce a broadening of the peak base for the most intense reflections. This broadening of the peak base is an indicator of the presence of locked particles, even at those fine sizes.
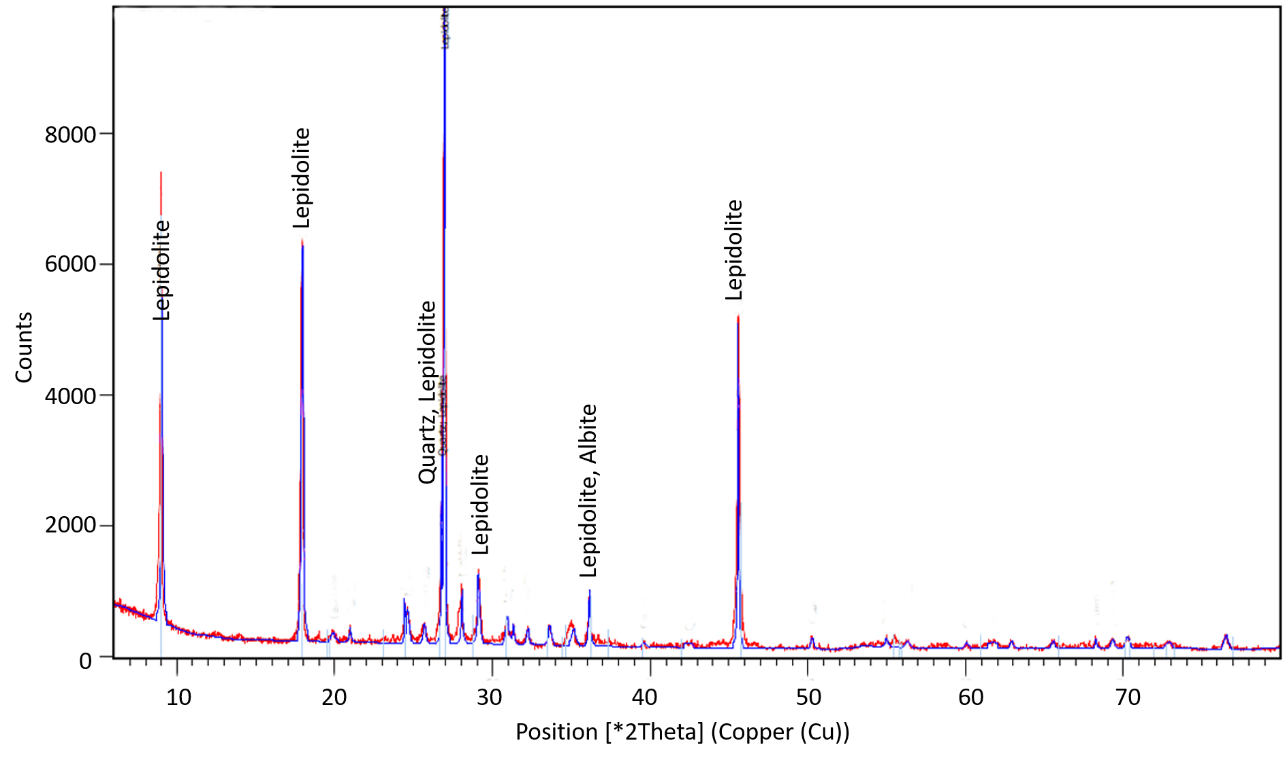
5. Conclusion
Despite the geological and mineralogical differences between Länttä spodumene and Gonçalo lepidolite ores, the mineral processing of both samples was faced with the same bottleneck: very fine mineral inclusions inside the lithium minerals, which led to lithium final concentrates with grades lower than those expected, even when working at particle sizes < 150 µm. During the processing of both samples, it was not possible to achieve a Li2O grade close to the Li2O content of the lithium minerals in study, even for low metal recoveries: for lepidolite, 4.50 % Li2O was the maximum grade obtained, and spodumene flotation exhibited a maximum grade of 5.20 % Li2O. It is important to notice that these grades are acceptable for the lithium metallurgy, meaning that they are not a matter of concern for the mining companies; however, it should be underlined that, for both cases, the impossibility of attaining grades close to the lithium mineral stoichiometry, is due to the ore very specific mineralogical features, rather than to any flotation inefficiencies, clearly demonstrating that these techniques are efficient tools to evaluate these types of micro-textures.
Mineralogical studies, using optical microscopy and SEM observations, XRD and Raman analyses, showed that, in the case of Länttä, spodumene occurs with fine quartz intergrowths and is crosscut by fine albite and K-feldspar to some extent, whilst microinclusions of quartz and albite were found in the Gonçalo lepidolite.
If the textural aspects of the lithium-rich mineral assemblage resultant from the petrogenetic conditions observed in the two studied cases are widespread through the pegmatitic orebodies, one should be aware of possible high difficulties to reach high-lithium grades in the flotation concentrates, unless very fine grinding, far below 0.075 mm, is reached. In this case, a decrease in the flotation efficiency and entrainment of very fine particles is expected, which would rule out this degree of fineness of grind. More selective comminution methods, as innovative electro-fragmentation techniques could be a potential solution for this problem, as they can promote preferentially fragmentation along grain boundaries enhancing mineral liberation. In addition, hydro and bioleaching processes can potentially evolve as alternatives for upgrading concentrates of lower Li2O content.
Acknowledgments
All the authors acknowledge the European Union’s Horizon 2020 research and innovation programme for Project FAME (Flexible and Mobile Economic Processing Technologies - grant agreement No. 641650) and also FELMICA and Keliber Oy for providing the investigated samples. Authors V. Ramos, A. Guedes and F. Noronha also acknowledge the funding by COMPETE 2020 through the ICT project (UID/GEO/04683/2013) with POCI-01-0145 reference - FEDER-007690 and also the CEMUP for performing SEM/EDS analyses. Author R. Sousa also acknowledges the “Fundação para a Ciência e Tecnologia” for financing the scholarship programme with the reference SFRH/BD/114764/2016. The Anonymous Reviewers are acknowledged for their constructive remarks that helped to improve the manuscript.
References
[1] B. Swain, “Recovery and recycling of lithium: A review,” Separation and Purification Technology, vol. 172, pp. 388-403, 2017. View Article
[2] B. Levich, “A five year strategic outlook for the lithium industry,” in Metal Bulletin, London, 2009.
[3] J. S. Kim, K. W. Chung, J. Y. Lee and S. D Kim, “Method for preparing high-purity lithium carbonate from brine,” EP2641870 A4, 2014. View Article
[4] H. Kim, J. Hong, N.Y. Park, S.W. Kim and K. Kang, “Aqueous recharchable Li and Na ion batteries,” Chemical Reviews, vol. 144, pp. 788-827, 2014.View Article
[5] S. Salil, “Nickel Zinc (NiZn) battery technology overview for micro hybrid application,” in PowerGenix, B.P. Magazine, Ed., 2012.View Article
[6] R. O. Bach, “Lithium current applications in science, medicine and technology,” in Southeastern Regional Meeting, A.C. Society, Ed.: Wiley, 1985.View Article
[7] A. Chagnes and J. Swiatowska, Lithium process chemistry: resources, Extraction, batteries, and recycling. Elsevier Science, 2015. View Article
[8] S. S. Penner, Lithium Needs and Resources. Corning: New York, 1977. View Article
[9] J. B. Goodenough and K.S. Park, “The Li-ion rechargeable battery: a perspective,” J. Am. Chem. Soc., vol. 135, pp. 1167-1176, 2013.View Article
[10] B. Dunn, H. Kamath and J. M. Tarascon, “Electrical energy storage for the grid: a battery of choices,” Science, vol. 334, pp. 928-935, 2011.View Article
[11] S. Reichel, T. Aubel, A. Patzig, E. Janneck and M. Martin, “Lithium recovery from lithium-containing micas using sulfur oxidizing microorganisms,” Miner. Eng., vol. 106, pp. 18-21, 2017.View Article
[12] U.S. Geological Survey. (2018, June 20). Mineral Commodity Summaries. [Online]. Available: https://www.statista.com/statistics/268789/countries-with-the-largest-production-output-of-lithium/ View Article
[13] R. L. Rudnick and S. Gao, “Composition of the continental crust,” Treatise on Geochemistry, vol. 4, pp. 1-51, 2014.View Article
[14] D. Sadoway, “Toward new technologies for the production of lithium,” JOM, vol. 50, pp. 24-26. 1998.View Article
[15] M. Stone, An accounting of the materials flows for lithium. Technical Report, Carnegie Institute of Technology at Research Showcase @ CMU, pp. 22, 1995. View Article
[16] D.E. Garret, Handbook of lithium and natural calcium chloride (1st ed.), Elsevier Academic Press: Amsterdam, Boston, 2004.View Article
[17] F. Brandtand R. Haus, “New concepts for lithium minerals processing,” Minerals Engineering, vol. 23, pp. 659-661, 2010.View Article
[18] M. M. Amarante, A. Botelho de Sousa and M. Machado Leite, “Processing a spodumene ore to obtain lithium concentrates for addition to glass and ceramic bodies,” Minerals Engineering, vol. 12, pp. 433-436, 1999.View Article
[19] J. Lessard, J. Bakker and L. McHugh, “Development of ore sorting and its impact on mineral processing economics,” Minerals Engineering, vol. 65, pp. 88-97, 2014. View Article
[20] M. C. Fuerstenau, J. D. Miller and M. C. Kuhn, Flotation fundamentals. Marcel Dekker Inc.: New York and Basel, 1985.
[21] J. Noronha, Viabilidade técnica da valorização de um minério de ambligonite da Argemela através de flutuação por espumas, Master Thesis, University of Porto, 2010.View Article
[22] M. Menéndez, A. Vidal, J. Toraño and M. Gent, “Optimisation of spodumene flotation,” The European Journal of Mineral Processing and Environmental Protection, vol. 4, pp. 130-135, 2004.View Article
[23] O. Sarapää, N. Kärkkäinen, T. Ahtola and T. Al-Ani, “High-tech metals in Finland,” in Mineral Deposits of Finland, W.D. Maier, R. Lahtinen and H. O’Brien, Eds., Elsevier, 2015, pp. 613-632.View Article
[24] R. Alviola, I. Manttari, H. Makitie, M. Vaasjoki, “Svecofennian rare-element granitic pegmatites of the Ostrobothnia region, Western Finland: Their metamorphic environment and time of intrusion,” Geological Survey of Finland, pp. 9-29, 2001. View Article
[25] P. Černý and T.S. Ercit, “The classification of granitic pegmatites revisited,” Canadian Mineralogist, vol. 43, pp. 2005-2026, 2005.View Article
[26] S. E. Kesler, P. W. Gruber, P. A. Medina, G. A. Keoleian, M. P. Eversion and T. J. Wallington, “Global lithium resources: Relative importance of pegmatite, brine and other deposits,” Ore Geology Reviews, vol. 48, pp. 55-69, 2012. View Article
[27] Keliber Oy. (2018, June 20). [Online]. Available: http://keliber.fi/2013 View Article
[28] O. Sarapää, N. Kärkkäinen, T. Ahtola and T. Al-Ani, “High-tech metal potential in Finland with emphasis on rare earth elements (REE), titanium and lithium,” Central European Geology, vol. 58, pp. 291–305, 2015.View Article
[29] A. M. R. Neiva and J. M. F. Ramos, “Geochemistry of granitic aplite-pegmatite sills and petrogenetic links with granites, Guarda-Belmonte area, central Portugal,” European Journal of Mineralogy, vol. 22, pp. 837-854, 2010.View Article
[30] J. M. F. Ramos, Locality nº5: Seixo Amarelo-Gonçalo rare element aplite-pegmatite field. In Granitic pegmatites: The state of the art - field trip guidebook. Memórias N.º9, A. Lima, E. Roda Robles Eds. Departamento de Geologia da Faculdade de Ciências Universidade do Porto: Porto, 2007, pp. 72-86.
[31] B. Charoy and F. Noronha, “Rare-Element (Li-rich) granitic and pegmatitic plutons: A primary or superimposed signature?,” Revista Brasileira de Geocências, vol. 29, pp. 3-8, 1999. View Article
[32] Lepidico. (2018, June 12). ASX/Media Announcement. [Online]. Available: http://www.lepidico.com/investors/announcements/ View Article
[33] S. M. Bulatovic, Handbook of Flotation Reagents: Chemistry, theory and practice - Flotation of Industrial Minerals, (1st ed.) Elsevier Science, 2007.View Article
[34] M. M. Amarante, A. M. B. Sousa, A. Oliveira, J. M. F. Ramos, J. C. Grade and M. Leite, “Processamento de Minérios de Lítio – Contribuição para a Valorização Tecnológica de Espodumenas e Petalites,” Relatório de projecto FCT, secção de Processamento de Matérias Primas, IGM, pp. 27, 2004.View Article
[35] C. Gibson, M. Aghamirian and T. Grammatikopoulos, “A review: The beneficiation of lithium minerals from hard rock deposits,” in Proceedings of the SME Annual Meeting, Denver, CO, 2017.View Article
[36] Sweco Industry Oy, “Pre-feasibility study,” Report, F13272, Keliber Lithium Project, pp. 215, 2016.
[37] R. J. Thomas, D. Biihmann, W. D. Bullen, A. J. Scogings and D. De Bruin, “Unusual spodumente pegmatites from the Late Kibaran of southern Natal, South Africa,” Ore Geology Reviews, vol. 9, pp. 161-182, 1994.View Article
[38] T. C. Martins, Multidisciplinary study of pegmatites and associated Li and Sn-Nb-Tamineralisation from de Barroso-Alvão region, PhD Thesis, University of Porto, pp. 192, 2009.View Article
[39] P. Černý, R. B. Ferguson, “The Tanco pegmatite at Bernico Lake, Manitoba. IV Petalite and spodumene relations,” Canadian Mineralogist, vol. 11, pp. 660-678, 1972. View Article