Volume 6 - Year 2020 - Pages 52-59
DOI: 10.11159/ijmmme.2020.006
Mechanical and Thermomechanical Behavior Of Sic/Si Compounds Subjected To Controlled Atmospheric Conditions
J.F. Gamarra-Delgado1, J.J. Paredes-Paz1, V.C. Bringas-Rodríguez1, D.L. Mayta-Ponce1, G.P. Rodríguez-Guillén1 and F.A. Huamán-Mamani1
1Grupo de Investigación en Ciencia y Tecnología de Materiales, Departamento de Ciencias Naturales, Universidad
Católica San Pablo, Arequipa, Perú
Urb. Campiña Paisajista, Quinta Vivanco s/n, Arequipa 04001, Perú
frank.gamarra23@gmail.com; janice.paredes@ucsp.edu.pe; veronicawnh@gmail.com; dlmayta@ucsp.edu.pe;
gprodriguez@ucsp.edu.pe; fhuaman@ucsp.edu.pe
Abstract - Biomorphic SiC/Si compounds were fabricated from copaiba wood (Copaifera officinalis, natural wood native to Peru), by reactive infiltration of molten silicon in a porous carbon preform obtained by a controlled pyrolysis process of wood. Structural and microstructural characterization tests by X-ray diffraction and scanning electron microscopy, respectively, revealed, on the one hand, the presence of crystalline phases of SiC, Si and C, and on the other, the typical morphology of this type of material, which it consists of a continuous SiC scaffold with elongated channels in the direction of tree growth and the presence of residual Si and C located mainly in the porosities of the material. The mechanical behavior in uniaxial compression was also studied at a constant compression rate of 0.05 mm/min and as a function of temperature (from ambient to 1400 ºC) and test atmosphere (ambient air, humid air, dry air, Ar, N2 and reducing mixture (95% Ar + 5% H2). The mechanical results were evaluated based on values of maximum stress and modulus of elasticity (stiffness), finding a clear reduction in the values of maximum stress and stiffness of the material when the samples passed of ambient test temperatures at 1400 ºC. On the other hand, mechanical tests in a controlled atmosphere were carried out at a constant temperature of 1100 ºC and the results showed that the mechanical behavior of the studied compounds is slightly influenced by the working atmosphere. Mechanical data found in the various test conditions will be an important support for the definition of the maximum allowable stress (considering the safety factor applied for a particular case) in the industrial application of the materials studied in this work.
Keywords: silicon carbide, mechanical resistance, controlled atmosphere, SiC / Si, copaiba, Copaifera officinalis
© Copyright 2020 Authors This is an Open Access article published under the Creative Commons Attribution License terms. Unrestricted use, distribution, and reproduction in any medium are permitted, provided the original work is properly cited.
Date Received: 2019-08-20
Date Accepted: 2020-09-21
Date Published: 2020-10-19
1. Introduction
The development of new engineering materials, mainly those that work in high temperature conditions, are currently in great demand. In this sense, the modern industry has seen in carbides an enormous potential to meet its highly demanding requirements regarding mechanical properties [1]. On the other hand, wood is a renewable resource with a unique cellular microstructure and whose architecture has been ranked by nature through the years. Wood has now become a very important precursor material for the development of new bio-inspired (biomorphic) materials, which take advantage of the good combination of mechanical resistance, toughness, rigidity and low density that most of the available timber species present. [2-9].
Most research work on carbides is currently focused on the fabrication and mechanical and functional characterization of biomorphic SiC and SiC/Si obtained from cellulosic precursors [3][12]. Today there are several methods for obtaining biomorphic carbides, but the most studied method is that of reactive infiltration of metallic silicon in a porous carbon preform, which stands out among other methods for proposing a feasible, scalable, environmentally friendly methodology and energy saving [3]. The process of obtaining carbides from wood involves a first stage of pyrolysis the wood to obtain a carbon preform that is then infiltrated with metallic elements such as Si, Ti, Ta, etc. The carbon preforms are obtained by a controlled thermal pyrolization process of the wood at temperatures above 800 ºC in an inert atmosphere (Ar, N2) [10][11], later the carbon preform is infiltrated with metallic elements considering a excess of these up to over 30% of the stoichiometric quantity necessary for the mass of carbon to infiltrate [12-16]
Biomorphic SiC and SiC/Si applications are wide and depend on their mechanical properties and pore structure, the most outstanding applications include: high temperature filters for gas or liquid, catalyst support, energy storage materials, barriers thermal, anti-wear surfaces, etc. [17-21]
The mechanical properties of SiC/Si compounds have been studied extensively [22-24], but mostly under ambient temperature and atmospheric conditions, however, only few studies have been directed at considering the atmosphere of work as a factor of great importance for the design of structures fabricated with SiC/Si. Therefore, the present study tries to show the effect of the change of working atmospheres in the maximum mechanical resistance and stiffness of SiC/Si composites.
2. Materials and Methods
SiC/Si composite materials were fabricated by reactive infiltration of metallic silicon in porous carbon preforms. Several authors have previously reported the detailed fabrication methodology for these materials [13]. In this work copaiba wood was selected as the main raw material, this wood species is classified as high density basic wood and is native to the Peruvian jungle. Cubes of approximately 10 mm on each side were cut from the selected wood and then dried at 80 ºC, then they were conducted to a pyrolysis process in an inert atmosphere up to the maximum temperature of 900 ºC with an isotherm time of 30 min. (Fig. 1 (a)).
The carbon preforms obtained after the pyrolysis were subjected to a reactive infiltration process under vacuum and at a maximum temperature of 1550 ºC for 30 minutes with an excess of silicon of 50% with respect to the stoichiometric amount for the amount of carbon to be infiltrated (Fig . 1 (b)).
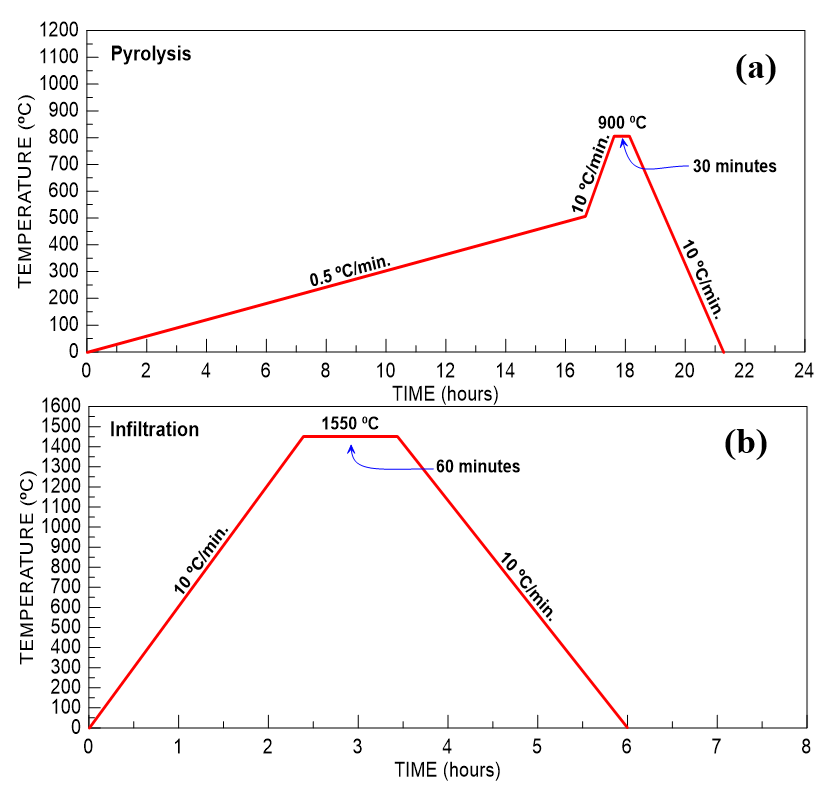
The structural characterization of the carbon preforms and of the SiC/Si compounds was carried out in an X-ray diffraction machine (Bruker, model D8 Endeavor, Germany) that has a Cu tube and Kα radiation (wavelength of 0.15405 nm). All tests were performed in the 2θ scanning range of 10º to 75º, with a step width of 0.02º and tube conditions of 35 kV and 40 mA.
Microstructural characterization was performed on polished carbon and SiC/Si surfaces using an AM SCOPE light microscope (50X - 500X ME320B-PZ, USA). Microstructural observations were made in reflection mode and on previously polished surfaces with grade 6, 3 and 1 micron diamond paste (in that order).
The mechanical characterization was carried out in a universal testing machine (MICROTEST, model EM1/50/FR, Spain) that has three interchangeable chambers that cover the range of test temperatures between -30 and 1500 ºC and has a hermetic system of control of atmospheres with which it is possible to carry out tests in environmental and non-ambient (inert, oxidizing or reducing) conditions. The mechanical tests were carried out in uniaxial compression at a constant compression rate of 0.05 mm/min and at variable temperatures between ambient and 1400 ºC. In addition, with the aim of evaluating the effect of non-environmental conditions on the mechanical response of the studied materials, tests were carried out at a constant temperature of 1100 ºC and in atmospheres of humid air, dry air, Ar, N2 and reducing mixture (95% Ar + 5% H2).
The samples used in the mechanical tests consisted of 5x5x10 mm parallelepipeds cut from larger samples with the help of a low speed precision cutter that has diamond edge discs. The force and displacement data obtained in the mechanical tests were converted to stress vs. strain graphs. The stress-strain curves allowed us to analyze and compare the values of maximum stress and moduli of elasticity of the materials studied under the various test conditions.
3. Results and Discussion
3.1. Structural and Microstructural Characterization
Fig. 2 shows the X-ray diffraction spectra for samples of carbon (Fig. 2 (a)) and of SiC/Si compounds (Fig. 2 (b)). The diffraction peaks identified in the carbon sample reveal the presence of graphite, however, considering the shape of the baseline of the diffraction spectrum, the carbon obtained could be considered as a mainly amorphous material. On the other hand, the diffraction spectrum of the SiC/Si compound confirms the presence of up to three crystalline phases: SiC, carbon (graphite) and Si. The shape of the baseline indicates that the SiC/Si compound after the infiltration process is completely crystalline and contains Si and C (graphite) residual.
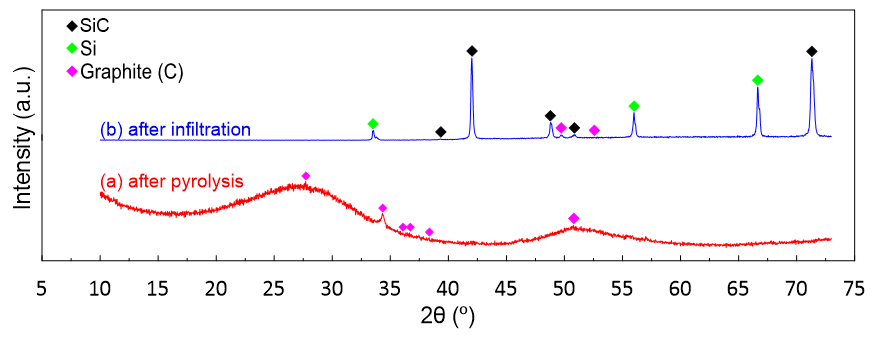
Fig. 3 presents the morphology found on the surfaces of carbon (Fig. 3 (a)) and SiC/Si compound (Fig. 3 (b)). Both microstructures are of the cross section (with respect to the growth direction of the tree) and are clearly defined. The carbon sample has a single phase of C, with the presence of some rough or less rounded regions in darker contrast that would correspond to pores distributed throughout the area of the micrograph, and are also elongated in the growth direction of the tree. On the other hand, on the polished surface of SiC/Si it was possible to observe up to four distinct phases: SiC (dark gray), Si (light gray), porosity (rounded black regions) and unreacted carbon (black regions no definite shape). The phases found microstructurally are in good agreement with the X-ray diffraction results presented in Fig. 2 of this work.

3.2. Mechanical Characterization
Fig. 4 presents stress vs. strain curves where a clear ratio of increase of the average maximum resistance is appreciated when increasing the amount of silicon in excess of 20 to 50% with respect to the stoichiometric molar ratio of the SiC molecule (Fig. 4 (a-c)). On the other hand, a systematic reduction of the average maximum resistance can be seen when the test temperature increases from room temperature to 1400 °C in the compound with 50% excess silicon (Fig. 4 (c-f)).
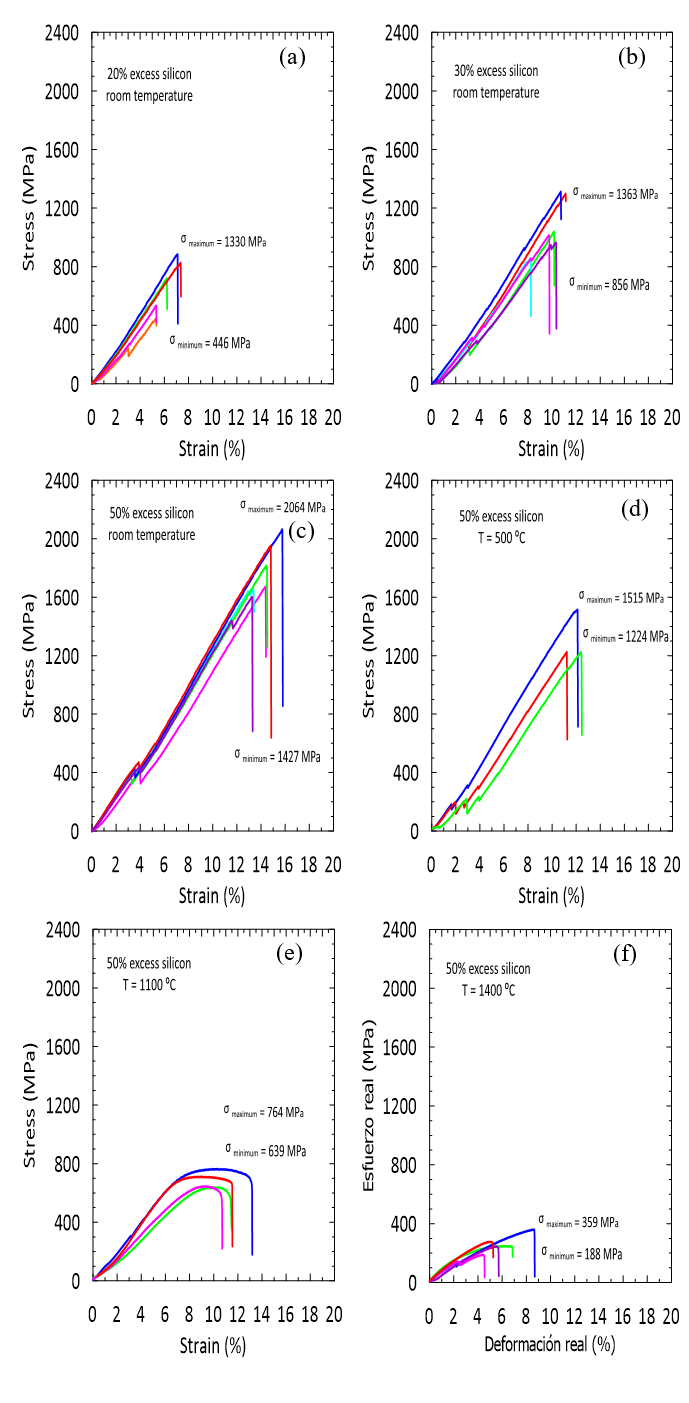
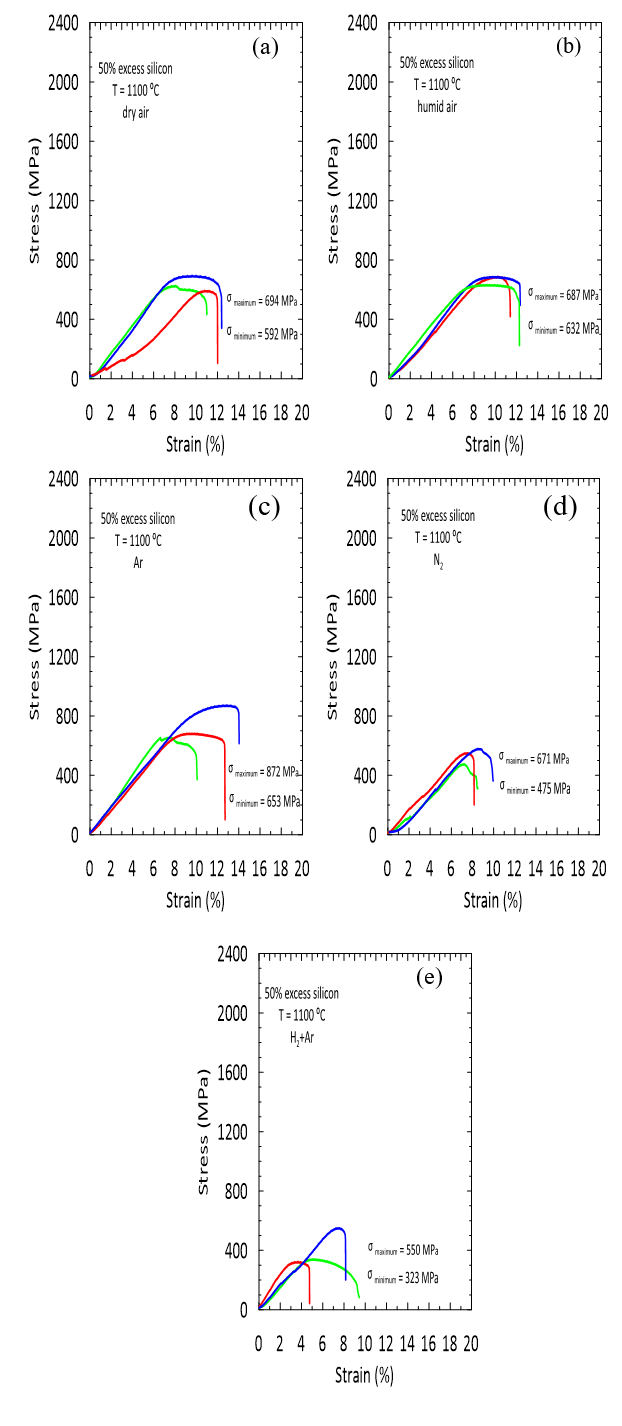
Fig. 5 shows stress vs. strain curves for SiC/Si compounds with 50% silicon in excess with respect to the stoichiometric composition of the SiC molecule. The tests were carried out in various types of atmospheres to verify the mechanical behavior (maximum resistance to compression and modulus of elasticity) of the materials studied under conditions in which they could work as part of industrial mechanical components. A greater sensitivity of the average maximum resistance in test atmospheres of N2 and H2 (5%) + Ar (95%) could be appreciated.
Table 1 presents a summary of the data obtained for the mechanical resistance and moduli of elasticity maximum of SiC/Si compounds evaluated in uniaxial compression and under variable conditions of temperature and atmosphere. It has been possible to verify a systematic reduction of the values of maximum stress and moduli of elasticity when the test temperature increases from room temperature to 1400 ºC. This result could be attributed to the presence of residual metallic silicon in the porosities of the SiC ceramic matrix. The metallic Si present in the SiC/Si compound tends to soften with increasing test temperature, this effect being more evident at temperatures close to the melting point of Si. The effect of this softening translates into a systematic reduction in the overall stiffness of the SiC/Si compound.
On the other hand, it has been possible to verify a slight relationship between the mechanical behavior of the SiC/Si compound and the test atmosphere, which suggests that the change of working atmosphere should be considered in the engineering design of components or products that Include the material studied in this work.
Table 1: Mechanical data found for SiC/Si tested under variable conditions of temperature and atmosphere
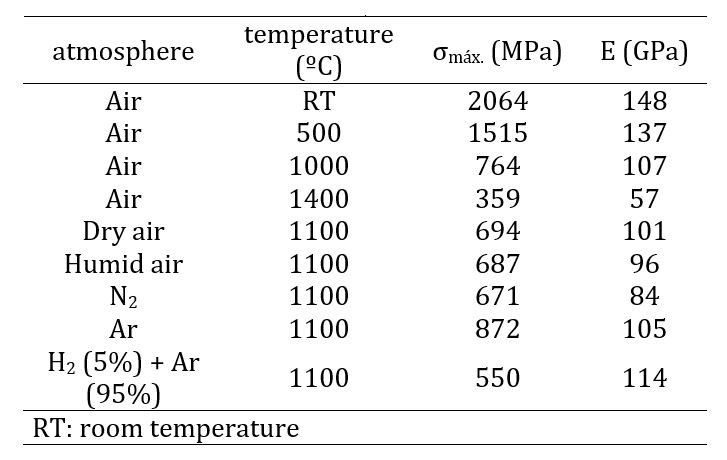
Fig. 6. shows the upper and lower limits found for the data set of maximum stresses and moduli of elasticity of SiC/Si compounds under conditions of variable temperature and test atmosphere. Fig. 6 (a) and 6 (b) show the influence of the test temperature on the average maximum stress and modulus of elasticity, respectively. A lower dispersion of values can be seen when the test is carried out at 1400 ºC, this observation could suggest that at temperatures of 1400 ºC the Si present in the compound contributes minimally to the overall mechanical response of the compound (being close to its melting point), which can be seen more clearly in Fig. 6 (a) In this scenario, only the mechanical response mechanisms of the SiC ceramic matrix take on importance for data analysis.

Another important aspect that deserves to be analyzed correctly can be seen in the tests at room temperature (RT) of Figs. 6 (a) and 6 (b), where the values found for the maximum stress are widely dispersed between 1427 and 2064 MPa, while the values for the modulus of elasticity only have a slight dispersion between 142 and 148 MPa. In this regard, it could be suggested that the dispersion of the maximum stress values is due to the fact that the appearance and propagation of cracks in the ceramic matrix (responsible for the maximum stress of the material) is variable and occurs at stresses above the proportional limit. . For its part, the modulus of elasticity has little dispersion at room temperature because this property is measured only in the elastic range before the limit of proportionality (before cracks appear).
Figs. 6 (c) and 6 (d) show the upper and lower limits for all the data found for maximum stress and moduli of elasticity of SiC/Si compounds tested in variable atmospheres. In this regard, previously we must mention that this group of tests were carried out at a constant temperature of 1100 ºC, since it was previously possible to confirm that at that temperature the material exhibited a completely fragile behavior and in this way only the test atmosphere could influence the mechanical behavior of the studied materials. The results found showed that the SiC/Si compounds were very mechanically stable in humid air and dry air atmospheres, with respect to their maximum stress, but under nitrogen and reducing atmospheric (95% Ar + 5% H2) conditions, their maximum stress was slightly reduced. The results of maximum stress in an inert atmosphere of Ar were on average the highest, this result could suggest that when the SiC/Si compound is in an inert environment it does not undergo any chemical change leading to the mechanical instability of the material. In the other test atmospheres it is possible that chemical changes occur that produce an effect on the final mechanical response of the materials, hence the importance of evaluating the dispersion of data to be able to suggest permissible design effort from the application that can be used give the studied material.
The comparative graph of the modulus of elasticity (E) as a function of the test atmosphere shown in Fig. 6 (d)) reveals that there is no clear or direct relationship between the test atmosphere and the stiffness of the materials studied in this work. Therefore, it could be suggested that the stiffness of the material is stable in various working environments.
4. Conclusions
SiC/Si compounds have been successfully fabricated from copaiba wood, following procedures established in the literature for wood pyrolysis in an inert atmosphere followed by reactive infiltration of metallic silicon in carbon preforms.
X-ray diffraction studies confirmed the presence of a mostly amorphous phase in samples of pyrolyzed wood (carbon preform) with low energy graphite peaks. On the other hand, it was found that the SiC/Si compounds obtained after the reactive infiltration process were completely crystalline with the presence of diffraction peaks of SiC, Si and C (graphite).
The microstructural studies were in good agreement with the data found in the DRX studies, showing a single homogeneous phase of carbon in the samples of pyrolyzed wood (with morphology similar to that of the cellulosic precursor) and four phases in the SiC/Si compounds. : SiC (dark gray), Si (light gray), residual carbon (black without defined shape) and pores (black with rounded shape).
Uniaxial compression studies showed a clear influence of the maximum stress and modulus of elasticity with the test temperature. It was found that as the test temperature increased, the studied materials became less rigid and presented less maximum stress. It is suggested that these results are due to the progressive softening of the remaining Si as the test temperature near the silicon melting point increases.
The mechanical data found in the controlled atmosphere tests showed that the studied materials are sensitive (respect to their maximum stress) to the change in working atmosphere, mainly in nitrogen and reducing mixture atmospheres (95% Ar + 5% H2). However, changes in atmosphere do not have a definitive effect on the stiffness of the materials studied. Both, the maximum stress and stiffness of the materials studied under conditions of variable temperatures and atmospheres must be considered to define the allowable stress of these materials in their probable industrial application.
Acknowledgements
This work was financed by the project Concytec - Banco Mundial, through its executing unit the Fondo Nacional de Desarrollo Científico, Tecnológico y de Innovación Tecnológica (Fondecyt) within the framework of call E041-01 with contract N° 36-2018-FONDECYT-BM-IADT-AV and was executed in the laboratories of the Universidad Católica San Pablo.
References
[1] Li, F., Liu, J., Huang, X., Zhang, G., “Porous Ultra-High Temperature Ceramics: Preparation, Structure and Properties”, J. of the Chin. Ceram. Soc., 46(12), pp. 1669-1684, 2018.
[2] Parlett, C.M.A., Wilson, K., Lee, A.F., “Hierarchical porous materials: Catalytic applications”, Chem. Soc. Rev., 42 (9), pp. 3876-3893, 2013. View Article
[3] Min Yu, Guo-jun Zhang, Theo Saunders, “Wood-derived ultra-high temperature carbides and their composites: A review”, Ceram. Inter., vol. 46, issue 5, pp. 5536-5547, 2020. View Article
[4] M.P. Wolcott, K. Englund, “A technology review of wood-plastic composites”, in 33rd Inter. Part. board/composite Mat. Sym. Proc., 1999.
[5] C.L. Huang, H. Lindström, R. Nakada, J. Ralston, “Cell wall structure and wood properties determined by acoustics—a selective review”, Holz Roh Werkst, 61(5), pp. 321-335, 2003. View Article
[6] R. Astley, J. Harrington, K. Stol, “Mechanical modelling of wood microstructure, an engineering approach”, Trans. Inst. Prof. Eng. N. Z. Electr. Mech. Chem. Eng. Sect., 24(1), pp. 21, 1997.
[7] S.C. Mayo, F. Chen, R. Evans, “Micron-scale 3D imaging of wood and plant microstructure using high-resolution X-ray phase-contrast microtomography”, J. of Struc. Biol., vol. 171, issue 2, pp. 182-188, 2010. View Article
[8] D.E. Kretschmann, “Mechanical properties of wood Environments”, 5, pp. 34, 2010.
[9] Jianwei Song, Chaoji Chen, Shuze Zhu, Mingwei Zhu, Jiaqi Dai, Upamanyu Ray, Yiju Li, Yudi Kuang, Yongfeng Li, Nelson Quispe, Yonggang Yao, Amy Gong, Ulrich H. Leiste, Hugh A. Bruck, J. Y. Zhu, Azhar Vellore, Heng Li, Marilyn L. Minus, Zheng Jia, Ashlie Martini, Teng Li, Liangbing Hu “Processing bulk natural wood into a high-performance structural material” Nat., 554 (7691), pp. 224, 2018. View Article
[10] C.E. Byrne, D.C. Nagle, “Carbonized wood monoliths Characterization” Carbon, 35 (2), pp. 267-273, 1997. View Article
[11] C.E. Byrne, D.C. Nagle, “Carbonization of wood for advanced materials applications”, Carbon, 35(2), pp. 259-266, 1997. View Article
[12] P. Greil, T. Lifka, A. Kaindl, “Biomorphic cellular silicon carbide ceramics from wood: II. Mechanical properties”, J. Eur. Ceram. Soc., 18(14), pp. 1975-1983, 1998. View Article
[13] P. Greil, T. Lifka, A. Kaindl, “Biomorphic cellular silicon carbide ceramics from wood: I. Processing and microstructure”, J. Eur. Ceram. Soc., 18(14), pp.1961-1973, 1998. View Article
[14] Dong‐Woo Shin, Sam Shik Park, Yong‐Ho Choa, Koichi Niihara, “Silicon/silicon carbide composites fabricated by infiltration of a silicon melt into charcoal”, J. Am. Ceram. Soc., 82(11), pp. 3251-3253, 1999. View Article
[15] C. Zollfrank, H. Sieber, “Microstructure and phase morphology of wood derived biomorphous SiSiC-ceramics”, J. Eur. Ceram. Soc., 24(2), pp. 495-506, 2004. View Article
[16] F.M. Varela-Feria, J. Martı́nez-Fernández, A.R de Arellano-López, M. Singh, “Low density biomorphic silicon carbide: microstructure and mechanical properties”, J. Eur. Ceram. Soc., 22(14), pp.2719-2725, 2002. View Article
[17] K. E. Pappacena, K. T. Faber H. Wang, W. D. Porter, “Thermal conductivity of porous silicon carbide derived from wood precursors”, J. Am. Ceram. Soc., 90(9), pp. 2855-2862, 2007. View Article
[18] P. González, J. Serra, S. Liste, S. Chiussi, B. León, M. Pérez-Amor, J. Martı́nez-Fernández, A.R. de Arellano-López, F.M. Varela-Feria, “New biomorphic SiC ceramics coated with bioactive glass for biomedical applications”, Biom., 24 (26), pp. 4827-4832, 2003. View Article
[19] M.P. Orihuela, A. Gómez-Martín, J.A. Becerra-Villanueva, J. Ramírez-Rico, J. Martínez-Fernández, “Comportamiento del SiC biomórfico como filtro de partículas en motores diésel de automoción” in LV Congr Nac La Soc Española Cerámica y Vidrio, 2016.
[20] M. Pilar Orihuela, Aurora Gómez-Martín, José A. Becerra, Ricardo Chacartegui, Joaquín Ramírez-Rico, “Performance of biomorphic Silicon Carbide as particulate filter in diesel boilers”, J. of Env. Man., vol. 203, part 3, pp. 907-919, 2017. View Article
[21] A. Gómez-Martín, M.P. Orihuela, J. Ramírez-Rico, R. Chacartegui, J. Martínez-Fernández, “Thermal conductivity of porous biomorphic SiC derived from wood precursors”, Ceram. Inter., vol. 42, issue 14, pp. 16220-16229, 2016. View Article
[22] Nataliya D. Shcherban, “Review on synthesis, structure, physical and chemical properties and functional characteristics of porous silicon carbide”, J. of Ind. and Eng. Chem., vol. 50, pp. 15-28, 2017. View Article
[23] M.A. Bautista, J. Quispe Cancapa, J. Martinez Fernandez, M.A. Rodríguez, M. Singh, “Microstructural and mechanical evaluation of porous biomorphic silicon carbide for high temperature filtering applications”, J. of the Eur. Ceram. Soc., vol. 31, issue 7, pp. 1325-1332, 2011. View Article
[24] Zili Yan, Jie Liu, Jianchun Zhang, Tian Ma, Zhengcao Li, “Biomorphic silicon/silicon carbide ceramics from birch powder”, Ceram. Inter., vol. 37, issue 3, pp.725-730, 2011. View Article