Volume 9 - Year 2023 - Pages 16-24
DOI: 10.11159.ijmmme.2023.003
Influence of Lanthanides on the Phase Composition of Portland cement Clinker Accessed by Thermodynamic Modelling
Ana Rita Damasceno Costa1, Luanne Bastos de Britto Barbosa1, Ana Paula Kirchheim2, Jardel Pereira Gonçalves1,3
1Federal University of Bahia (UFBA), Polytechnic School
Salvador, Brazil, 40210-630
rita.damasceno@ufba.br; luanneb@ufba.br
2Federal University of Rio Grande do Sul (UFRGS), Department of Civil Engineering
Porto Alegre, Brazil, 90035-190
anapaula.k@ufrgs.br
1Federal University of Bahia (UFBA), Interdisciplinary Centre of Energy and Environment (CIENAM)
Salvador, Brazil, 40170-115
jardelpg@ufba.br
Abstract - The development of sustainable production has motivated using alternative raw materials in Portland cement manufacture. Co-processing industrial by-products containing impurities can change the stability of the clinker phases. Several studies have explored the effect of minor elements in the clinkering process. However, the effect of lanthanides remains unclear. This class of elements has been scarcely investigated due to its limited content in conventional alternative materials. Nevertheless, the increasing co-processing of by-products from the oil industry containing lanthanides demands further investigations on the effects of these elements. Furthermore, using alternative raw materials demands extensive experimental programs and investing time and financial resources. In this context, this study uses thermodynamic modelling to evaluate the effect of lanthanides on Portland clinker production. Systems containing La, Ce, Eu, Gd, Pr, and Nd as oxides in up to 10 wt.% of clinker raw meal processed at 1200 and 1400 °C were simulated. Thermodynamic calculations were based on the Gibbs energy minimisation method and performed in the FactSage software. La, Pr, Eu, Nd, and Gd improved the clinker C3S content. This effect was more significant for up to 3 wt.% of added dopant. These elements stabilised C2(A,F) rather than C3(A,F), suggesting a possible application in manufacturing high-ferrite and sulphate-resistant cements. Ce2O3 promoted notably different behaviour on phase assemblage, decreased the C3S development, and depleted C2(A,F). The cubic perovskite was the main solid phase incorporating the lanthanides, forming LaAlO3, NdAlO3, PrAlO3, EuAlO3, or GdAlO3. According to thermodynamic modelling, the co-processing of raw materials containing lanthanides can be environmentally safe since the emission of polluting gases containing impurities was negligible even when co-processing 10 wt.% of lanthanide oxide in the clinker raw meal.
Keywords: Clinker, Cement, Thermodynamic modelling, Dopants, Lanthanides.
© Copyright 2023 Authors This is an Open Access article published under the Creative Commons Attribution License terms. Unrestricted use, distribution, and reproduction in any medium are permitted, provided the original work is properly cited.
Date Received: 2023-08-16
Date Revised: 2023-09-25
Date Accepted: 2023-10-04
Date Published: 2023-10-10
1. Introduction
The cement industry is responsible for high environmental impacts. The exploitation of natural raw materials can lead to resource depletion, deforestation, soil destabilisation, and other harmful effects [1]. In this scenario, the co-processing of industrial by-products in cement manufacture reduces the extraction of natural sources, promotes proper waste disposal, and often improves sustainability in production [2]. However, it is noteworthy that these by-products contain elements besides those essential for the Portland cement composition (Ca, Si, Fe, Al, O), which can alter the phase development during production.
Several studies have explored the co-processing of alternative raw materials in Portland clinker production [3]–[6]. This approach can improve manufacturing sustainability and product properties by optimizing clinker composition and burnability [7]. On the other hand, the presence of potentially contaminating elements can promote limitations in the production process on an industrial scale, change the stability of clinker phases, emission of polluting gases during clinkering, and contaminate the environment by the leaching of hazardous compounds [3], [8]. In this sense, the co-processing of alternative raw materials should always be associated with studying the effects of impurities in the clinker phase assemblage and the environmental risk assessment.
The solidification of metals in clinker was reported as altered by the added content, industrial technology, processing time, and other impurities [9], [10]. The presence of non-metals can reduce the stabilisation temperature of Ca2SiO4 polymorphs, altering the hydraulicity of the cement and the mechanical properties of the pastes [11]. Several studies have investigated the effect of alkaline and transition metals on the stability of aluminates and their polymorphs [12], [13]. Although extensive research has been carried out on the effect of metals and non-metals on clinker, the presence of lanthanides needs further investigation.
The limited number of research on the influence of lanthanides in clinker production was justified by the restricted contents of these elements in ordinary alternative materials (< 0.1 wt.%) [14]. However, the increasing volume of waste from the oil industry being co-processed in cement kilns in recent years demands new investigations addressing the effect of these impurities on clinkering and gas emissions. As an example, lanthanum and cerium oxides comprised up to 5.1 and 1.6 wt.% of the spent fluid catalytic cracking catalyst (SFCC), respectively [15], [16]. SFCC was co-processed in previous investigations to replace bauxite in clinker production [4]–[6]. Nevertheless, the findings examine neither the effects of lanthanides on the clinker mineralogical composition nor their emission potential during clinkering.
Understanding the action mechanisms of lanthanides can be technologically challenging. It demands the execution of an extensive and complex experimental program, consuming financial resources, and time. In this sense, thermodynamic modelling is a useful solution. It applies the Gibbs energy minimisation principle to estimate the clinker composition throughout manufacturing. Previous investigations have established it as an accurate tool for phase determination [17], [18]. Modelling allows for optimizing experimental approaches by analysing the effect of dopants on the composition of solid, liquid, and gaseous phases along clinkering [19]–[21]. It was applied to evaluate the effect of FeO, K2O, MgO, Na2O, SiO2, SO3, and TiO2 [22]–[24]. However, further investigations could broaden the understanding of the effect of lanthanides incorporated in clinker raw meals due to the co-processing of alternative raw materials.
In this sense, this study applies thermodynamic modelling to investigate the influence of lanthanides on Portland clinker production. The effects of impurities on the stability of silicates and aluminates were investigated, in addition to the formation of new compounds and the polluting gases emission.
2. Methodology
2. 1. Thermodynamic modelling
Thermodynamic modelling was adopted to estimate the mineral composition of the clinkers produced in the theorical study. The software FactSage version 8.2 were applied to simulations. It contains optimised model parameters for the Gibbs free energy minimisation of solution phases to clinker equilibrium calculations [19]. Thermodynamic databases for gaseous components (FactPS) and oxides in solid, liquid, and solution phases (FToxid) were used for calculating the phase assemblage during production [19], [20]. The system pressure was fixed at 1 atm and the firing temperature was 1400 °C. As input data, the composition of clinker raw meal for an ordinary Portland cement (OPC) (69.5% CaO, 22.0% SiO2, 5.0% Al2O3, and 3.5% Fe2O3) was used. The lanthanides were added individually as oxides (La2O3, Ce2O3, Eu2O3, Gd2O3, Pr2O3, and Nd2O3) in up to 10 wt.% of the raw meal in 0.5 wt.% increments. The influence of dopants on the phase assemblage was evaluated at 1200, 1300, and 1400 °C during clinkering. The processing was applied using the software Equilibrium module and adopting the entire set of products available in the system. Calcium silicates are quantified as Ca3SiO5 (C3S) and Ca2SiO4 (C2S). Thermodynamic modelling using FactSage considers solid solutions of calcium aluminium ferrites, such as Ca2(Al,Fe)2O5 (C2(A,F)) and Ca3(Al,Fe)2O6 (C3(A,F)) [17], [19], [20]. Where (Al,Fe) means Al and Fe are variable in the structure. The modelled solid solution C2(A,F) is mainly associated with the OPC ferrite content, Ca2(AlxFe1-x)2O5, often named as C4AF [25]. The tricalcium aluminate or C3A (Ca3Al2O6) content is included in the C3(A,F) solid solution, and the complementary content corresponds to intermediate phases in the development of C4AF [20]. Thermodynamic modelling allowed quantifying other solids, including free calcium oxide (CaO) and new compounds formed from the chemical combination of lanthanides (LaAlO3, NdAlO3, PrAlO3, EuAlO3, GdAlO3, Gd4Al2O9, CeO2, Ce6O11, and Ce18O31) [19]. The calculated liquid phase corresponded to the melt phase content formed during clinkering. The melt fraction is mainly developed through the melting of aluminates (Ca(Al,Fe)2O4, Ca2(Al,Fe)2O5 and Ca3(Al,Fe)2O6) from 1250 °C, reaching their maximum at the final clinkering temperature and then resolidifying during clinker cooling [14], [25].
FactSage is the software with the broadest database for thermodynamic modelling of reactions at high temperatures [26]. The accuracy of thermodynamic calculations has been reported in previous investigations that simulated the clinkering process. The results were experimentally validated in the following applications: Influence of bauxite residue co-processed in Fe-rich calciumsulfoaluminate-ferrite clinker (CSAF) [27]; Effects of co-processing impurities, including MgO, ZnO, Cr2O3, and NiO in different zones of an industrial rotary kiln [28]; Influence of the kiln atmosphere on the quality of clinker produced on an industrial scale [21]; Effects of impurities containing phosphorus on the stability of silicates in clinker [20]; Valorisation of blast furnace slag in clinker production [29]; Effect of mineralising agents (CaF2, AlF3, MgSiF6, Na2SiF6, CaCl2, ZnO, and CaSO4) on clinker production [24]; Influence of the gradual substitution of Al2O3 with Fe2O3 in the raw material of an ordinary Portland clinker [30]. In this regard, all these applications have demonstrated that thermodynamic modelling results in better agreement with the phase composition of real clinkers compared to estimations from Bogue equations. These findings demonstrate the value of thermochemical calculations as an important tool for expanding the understanding of clinker production.
This study focused on analysing the effect of lanthanides during heating on clinker production (1200, 1300, and 1400 °C). The emission of compounds containing lanthanides was identified by quantifying gaseous phases during clinkering at 1400 °C through thermodynamic calculations on FactSage.
3. Results and discussions
3. 1. Composition of an Ordinary Portland Clinker (OPC) during heating
Table 1 presents the composition of an OPC at different temperatures to illustrate the phase evolution in an undoped system. Tricalcium silicate (C3S) is the main phase of OPC, responsible for the early-age compressive strength of hydrated cement [2]. It is formed during clinkering after 1250 °C and obtained through the reaction between dicalcium silicate (C2S) and calcium oxide (CaO) [14]. C2S is generally the first silicate formed in clinkering. This compound increases the later-age compressive strength of cementitious materials [2]. Modelling using FactSage identifies its gamma (T < 735 °C), alpha prime (735~1435 °C), and alpha (T > 1435 °C) polymorphs [25]. If the system has free CaO, it combines with C2S at about 1280 °C to form C3S [14]. This reaction is verified in Table 1, where CaO is depleted at 1300 and 1400 °C as C3S increases.
During heating, the proportion of C3(A,F) tends to be higher than C2(A,F). However, previous investigations have shown that this ratio tends to reverse during cooling [17]. The reason is the combination of CaO dissolved in the melt phase with C2S forming additional C3S [14]. Thereby, Ca availability is reduced for aluminates, promoting the formation of C2(A,F) instead of C3(A,F). In this sense, although the modelled OPC has a high content of C3(A,F) during heating at 1200 and 1400 °C, the system tends predominantly to form C2(A,F) during cooling [17]. At 1400 °C, C2(A,F) and C3(A,F) reached the melting point and then were converted to the melt phase.
Table 1. Predicted ordinary Portland clinker composition (wt.%) during clinkering at 1200, 1300 and 1400 °C.
Composition |
Phase |
1200 °C |
1300 °C |
1400 °C |
Ca3SiO5 |
C3S |
0.00 |
68.64 |
76.26 |
Ca2SiO4 α’ |
C2S α’ |
63.07 |
11.29 |
3.39 |
Ca2(Al,Fe)2O5 |
C2(A,F) |
2.36 |
1.59 |
0.00 |
Ca3(Al,Fe)2O6 |
C3(A,F) |
17.54 |
18.48 |
0.00 |
CaO |
CaO |
17.03 |
0.00 |
0.00 |
Melt |
Melt |
0.00 |
0.00 |
20.35 |
3. 2. Composition of lanthanide-doped clinkers at 1200 °C
Previous investigations established that the lanthanides would act similarly on the stability of the clinker phases due to their comparable atomic characteristics [14]. However, thermodynamic modelling indicated that Ce promotes notably different behaviours on the phase evolution during clinkering. On the other hand, La, Pr, Eu, Gd and Nd indeed have similar trends. Figure 1 shows the effect of lanthanide type and content on the phase assemblage during clinkering at 1200 °C. Figure 1a presents the data for La e as a representation of Pr, Eu, Gd, and Nd for simplification purposes, as the effect of these other lanthanides was similar.
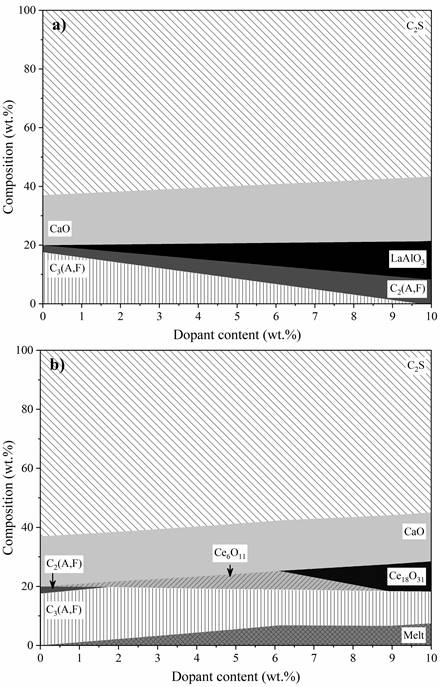
La, Pr, Eu, Gd, and Nd stabilised C2(A,F) rather than C3(A,F). Clinkers start from 2.4 wt.% C2(AF) and reach up to 8.2 wt.% when the dopant content is maximised (Figure 2a). For C3(AF), the content varies from 17.5 wt.% to values below 1.1 wt.%. This behaviour indicates that the presence of lanthanides promotes the formation of clinkers rich in C4AF. This characteristic is particularly promising for producing high ferrite clinker, in which the C3A content is limited, to guarantee the requirements of resistance to abrasion and attack by sulphates [31]. The evolution of calcium aluminium-ferrite according to the Ce2O3 content stands out among the analysed lanthanides (Figure 2b). Ce destabilised C2(A,F) by depleting it when 1.8 wt.% Ce2O3 was added. C3(A,F) is partially reduced as the dopant increases. Ce acted as a flux, lowering the melting point, and gradually increasing the melt phase content up to 6.1% Ce2O3.
Co-processing impurities in cement kilns promote the formation of compounds beyond those commonly found in OPC. Figure 1 presents the new solid phases of the modelled systems with up to 10 wt.% of dopants. La, Pr, Eu, Gd, and Nd were incorporated as cubic perovskite containing Al and O. The doped systems indicated the formation of LaAlO3, PrAlO3, EuAlO3, GdAlO3, and NdAlO3 with increasing values as the dopant content is increased. Previous investigations reported the formation of cubic lanthanum aluminate at temperatures above 540 °C [32], which can be pseudo-cubic or rhombohedral under industrial conditions [33]. Although the modelled structure of PrAlO3 was cubic, this compound has the highest number of crystalline structure transitions among rare earth perovskites [34]. NdAlO3 and GdAlO3 were classified as materials with high optical conductivity, applicable in producing optical amplifiers and solar panels [35], [36]. For Gd, doping above 8 wt.% resulted in the destabilisation of GdAlO3 and the formation of Gd4Al2O9. This phase was synthesised in previous research by processing Gd2O3 and Al2O3 at temperatures ranging between 1400 and 1700 °C [37]. Gd4Al2O9 is classified as an enhancer of the mechanical properties of ceramic materials, including the toughness and fracture strength of brittle ceramics [38].
Although the thermodynamic database includes the cerium aluminate perovskite [19], the simulations did not identify it (Figure 1b). Previous studies have shown that the combining potential of Ce in structures containing aluminium depends on several factors, including processing in a reducing atmosphere, pressure of O2 in the atmosphere, proportion of other impurities in the reagents, and heat treatment conditions [39]–[41]. Thermodynamic calculations showed Ce2O3 did not react with Al2O3 in the clinker raw meal, remaining in its pure crystalline forms and varying as the dopant content increased (CeO2, Ce6O11, and Ce18O31). Additional experimental investigations are necessary to understand the Ce action mechanism during clinkering and the formation of new solid compounds containing this element.
3. 3. Composition of lanthanide-doped clinkers at 1400 °C
The phase evolution at 1400 °C as a function of the dopant increment shows that La, Pr, Eu, Gd, and Nd enhanced C3S formation (Figure 2a).
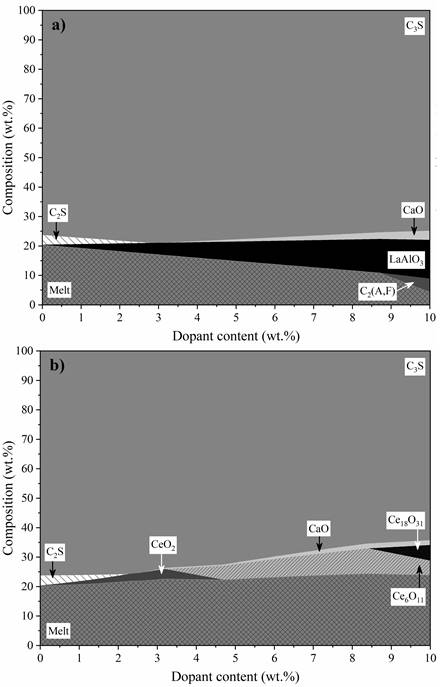
Up to 3% dopant, the C3S content shows a positive development rate, starting from 76.3 wt.% (0% dopant) and reaching up to 79.0 wt.% (3% dopant). This behaviour is related to the C2S destabilisation, which starts from 3.4 wt.% and is depleted in this range (Figure 2a). In this sense, lanthanides improve the clinker composition, increasing the C3S content by optimizing the reaction between C2S and CaO dissolved in the melt phase. A similar effect was observed in experimental samples doped with Praseodymium (Pr) [42].
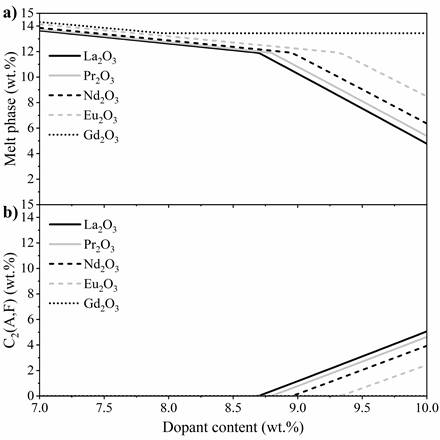
After 3 wt.% dopant, the C3S content decreased gradually, reaching 74.9 wt.% when 10 wt.% dopant was added. However, it is noteworthy that this percentage was improved, since the system produced 98% of the reference C3S amount (instead of 90%) even with 10 wt.% substitution of raw materials by lanthanides. In this range, the depletion of C2S limits the C3S growth. After 8 wt.% dopant, part of the melt phase recrystallised as C2(A,F). The results do not fully explain the recrystallisation occurring at high lanthanide contents. There are no lanthanides in the melt phase. Furthermore, resolidification occurs at different levels for each dopant, starting at 8.7 wt.% for La2O3, followed by Pr2O3 (8.8 wt.%), Nd2O3 (9.0 wt.%), and Eu2O3 (9.3 wt.%) (Figure 3). In this sense, high levels of this oxides (8~10%) increased the melting point of the clinker raw meal, promoting a considerably lower content of the melt phase at 1400 °C.
Cerium promoted discrepant effects compared to the analysed lanthanides (Figure 2b). Although the system started with the same C2S content (3.4 wt.%) and it was depleted in advance (occurring at 2.3 wt.% Ce2O3), the C3S content declined for increasing dopant levels. It reached 64.3 wt.% when 10 wt.% Ce2O3 was added, i.e., 84% of the calculated C3S for OPC (76.3 wt.%). This decrease may be related to the SiO2 destabilisation. In this sense, C3S tends to decompose into solid CaO and molten SiO2. The increased free CaO and melt in the C3S depletion regions evidenced this behaviour (Figure 2b).
3. 4. Emissions
Table 2 quantifies the emission of potentially polluting gases containing lanthanides accessed by thermodynamic modelling.
Table 2. Emission of compounds containing lanthanides simulated by thermodynamic modelling of the clinkering of raw meals containing 10 wt.% lanthanide oxide (1400 °C).
Lanthanide |
Compound |
Emission (µg/t of clinker) |
La |
La |
5.7 10-22 |
La2 |
9.8 10-48 |
|
LaO |
1.0 10-7 |
|
La2O |
8.1 10-31 |
|
La2O2 |
8.6 10-18 |
|
Pr |
Pr |
2.6 10-20 |
PrO |
1.7 10-6 |
|
Eu |
Eu |
2.6 10-12 |
EuO |
8.1 10-7 |
|
Eu2O |
1.4 10-22 |
|
Eu2O2 |
4.6 10-14 |
|
Nd |
Nd |
1.7 10-19 |
NdO |
1.1 10-7 |
|
NdO2 |
43.16 |
|
Gd |
Gd |
5.8 10-21 |
All dopants showed negligible emission levels. Nd had the highest emission potential. However, the volatilised phase (NdO2) was in the order of micrograms per ton of clinker produced, a value easily mitigated by the protection infrastructure of industrial kilns. On the other hand, the modelling did not detect the emission of gases containing Ce. This behaviour was attributed to the stability of its oxides as solid phases, as discussed in the previous section. For La, Pr, and Eu, the emission tended to higher values when the oxidation state of these elements was 2+. According to the modelling, the emission of polluting gases containing lanthanides does not promote environmental risk since the emissions were approximately zero even when co-processing 10 wt.% of lanthanide oxide in the clinker raw meal.
4. Conclusions
According to the results of this study, the following conclusions can be drawn:
La, Pr, Eu, and Nd showed similar effects, enhancing the C3S content. This effect occurred on a larger scale for up to 3 wt.% of added dopant, when C2S is depleted in the clinker. Ce promoted notably different behaviours on phase assemblage, decreasing the C3S development depending on the dopant content.
Increasing lanthanide content generally stabilised C2(A,F) rather than C3(A,F), suggesting that these elements may be applicable to produce high-ferrite and sulphate-resistant cements.
Co-processing lanthanides promoted the formation of new compounds, mainly the cubic perovskite containing Al and O (LaAlO3, NdAlO3, PrAlO3, EuAlO3, and GdAlO3), with increasing values as the dopant content is increased. However, Ce2O3 remained in its pure crystalline forms, varying as the dopant content increased (CeO2, Ce6O11, and Ce18O31).
The emission of polluting gases containing lanthanides was low even when co-processing 10 wt.% of lanthanide oxide in the clinker raw meal. However, it needs to be compared with the limits of the environmental regulations of each location. Furthermore, investigations are needed to understand how impurities could be immobilised in the cementitious material.
Acknowledgements
The authors express their sincere appreciation to the Bahia State Research Support Foundation (FAPESB, Brazil - Grant number 0289/2020 to A.R.D.C.) and the Coordination for the Improvement of Higher Education Personnel (CAPES, Brazil - Grant number 88887.608021/2021-00 to L.B.B.B.) for their financial support. J.P.G. and A.P.K. gratefully acknowledge the National Council for Scientific and Technological Development (CNPq, Brazil) and the Foundation for Research Support of the State of Rio Grande do Sul (FAPERGS, Brazil).
References
[1] K. S. Kumar, "Environmental impact assessment of a Proposed Bauxite mining using Rapid Impact Assessment Matrix Method", International Journal of Applied Environmental Sciences, vol. 5, no 1, p. 29-38, 2010, [Online]. Available: View Article
[2] S. P. Deolalkar, Designing Green Cement Plants. Oxford: Butterworth-Heinemann (Elsevier), 2016. doi: 10.1016/c2014-0-00783-6. View Article
[3] A. A. Bogush, J. A. Stegemann, Q. Zhou, Z. Wang, B. Zhang, T. Zhang, W. Zhang, and J. Wie, "Co-processing of raw and washed air pollution control residues from energy-from-waste facilities in the cement kiln", Journal of Cleaner Production, vol. 254, maio 2020, doi: 10.1016/j.jclepro.2019.119924. View Article
[4] S. R. C. Matos, P. R. de Matos, J. S. Andrade Neto, C. E. M. Campos, A. P. Kirchheim, e J. P. Gonçalves, "Synthesis and hydration of ye'elimite-containing cement (YCC) produced with spent fluid catalytic cracking catalyst", Construction and Building Materials, vol. 359, dez. 2022, doi: 10.1016/j.conbuildmat.2022.129364. View Article
[5] K. L. Lin, K. W. Lo, M. J. Hung, T. W. Cheng, e Y. M. Chang, "Recycling of spent catalyst and waste sludge from industry to substitute raw materials in the preparation of Portland cement clinker", Sustainable Environment Research, vol. 27, p. 251-257, set. 2017, doi: 10.1016/j.serj.2017.05.001. View Article
[6] H. Al-Dhamri e K. Melghit, "Use of alumina spent catalyst and RFCC wastes from petroleum refinery to substitute bauxite in the preparation of Portland clinker", Journal of Hazardous Materials, vol. 179, p. 852-859, jul. 2010, doi: 10.1016/j.jhazmat.2010.03.083. View Article
[7] D. N. Huntzinger e T. D. Eatmon, "A life-cycle assessment of Portland cement manufacturing: comparing the traditional process with alternative technologies", Journal of Cleaner Production, vol. 17, p. 668-675, maio 2009, doi: 10.1016/j.jclepro.2008.04.007. View Article
[8] M.-Y. Lee, Y.-J. Kim, D.-G. Hwang, Y.-Y. Kang, S.-K. Shin, e T.-W. Jeon, "Potential risk of exposure to heavy metals from co-processing of secondary wastes in the Republic of Korea", Journal of Environmental Management, vol. 286, maio 2021, doi: 10.1016/j.jenvman.2021.112164. View Article
[9] L. Blois e A. Lay-Ekuakille, "Environmental impacts from atmospheric emission of heavy metals: A case study of a cement plant", Measurement: Sensors, vol. 18, dez. 2021, doi: 10.1016/j.measen.2021.100313. View Article
[10] L. Wang, X. Huang, X. Li, X. Bi, D. Yan, W. Hu, C. J. Lim, and J. R. Grace, "Simulation of heavy metals behaviour during Co-processing of fly ash from municipal solid waste incineration with cement raw meal in a rotary kiln", Waste Management, vol. 144, p. 246-254, maio 2022, doi: 10.1016/j.wasman.2022.03.031. View Article
[11] S. Saidani, A. Smith, Y. el Hafiane, e L. ben Tahar, "Role of dopants (B, P and S) on the stabilization of β-Ca2SiO4", Journal of the European Ceramic Society, vol. 41, p. 880-891, jan. 2021, doi: 10.1016/j.jeurceramsoc.2020.07.037. View Article
[12] A. B. Ghazi, A. Jamshidi-Zanjani, e H. Nejati, "Clinkerisation of copper tailings to replace Portland cement in concrete construction", Journal of Building Engineering, vol. 51, jul. 2022, doi: 10.1016/j.jobe.2022.104275. View Article
[13] J. Zhu, Y. Chen, L. Zhang, B. Guo, G. Fan, X. Guan, and R. Zhao, "Revealing the doping mechanism of barium in sulfoaluminate cement clinker phases", Journal of Cleaner Production, vol. 295, maio 2021, doi: 10.1016/j.jclepro.2021.126405. View Article
[14] J. I. Bhatty, F. M. Miller, e S. H. Kosmatka, Innovations in Portland cement manufacturing, 2o ed. Skokie: Portland Cement Association, 2011. [Online]. Disponível em: View Article
[15] E. Restrepo, F. Vargas, E. López, e C. Baudín, "The potential of La-containing spent catalysts from fluid catalytic cracking as feedstock of mullite based refractories", Journal of the European Ceramic Society, vol. 40, p. 6162-6170, dez. 2020, doi: 10.1016/j.jeurceramsoc.2020.04.051. View Article
[16] Y. Xue, X. Wei, H. Zhao, T. Wang, e Y. Xiao, "Interaction of spent FCC catalyst and asphalt binder: Rheological properties, emission of VOCs and immobilization of metals", Journal of Cleaner Production, vol. 259, jun. 2020, doi: 10.1016/j.jclepro.2020.120830. View Article
[17] T. Hanein, F. P. Glasser, e M. N. Bannerman, "Thermodynamic data for cement clinkering", Cement and Concrete Research, vol. 132, jun. 2020, doi: 10.1016/j.cemconres.2020.106043. View Article
[18] D. Ariño Montoya, N. Pistofidis, G. Giannakopoulos, R. I. Iacobescu, M. S. Katsiotis, e Y. Pontikes, "Revisiting the iron-rich 'ordinary Portland cement' towards valorisation of wastes: study of Fe-to-Al ratio on the clinker production and the hydration reaction", Materials and Structures, vol. 54, no 30, 2021, doi: 10.1617/s11527-020-01601-w. View Article
[19] C.W. Bale, E. Bélisle, P. Chartrand, S. A. Decterov, G. Eriksson, A. E. Gheribi, K. Hack, I.-H. Jung, Y.-B. Kang, J. Melançon, A. D. Pelton, S. Petersen, C. Robelin, J. Sangster, P. Spencer, and M-A. V. Ende, "Reprint of: FactSage thermochemical software and databases, 2010-2016", CALPHAD, vol. 55, p. 1-19, 2016, doi: 10.1016/j.calphad.2016.07.004. View Article
[20] B. Hökfors, D. Boström, E. Viggh, e R. Backman, "On the phase chemistry of Portland cement clinker", Advances in Cement Research, vol. 27, no 1, p. 50-60, jan. 2015, doi: 10.1680/adcr.13.00071. View Article
[21] B. Hökfors, M. Eriksson, e E. Viggh, "Modelling the cement process and cement clinker quality", Advances in Cement Research, vol. 26, no 6, p. 311-318, nov. 2014, doi: 10.1680/adcr.13.00050. View Article
[22] M. Cantaluppi, N. Marinoni, F. Cella, A. Bravo, F. Cámara, G. Borghini, and W. Kagan, "An insight on the effect of sodium and silicon on microstructure and crystallography of high alumina cements", Cement and Concrete Research, vol. 148, out. 2021, doi: 10.1016/j.cemconres.2021.106533. View Article
[23] S. Cheng, M. Shevchenko, P. C. Hayes, e E. Jak, "Experimental phase equilibria studies in the FeO-Fe2O3-CaO-SiO2 system and the subsystems CaO-SiO2, FeO-Fe2O3-SiO2 in air", Metallurgical and Materials Transactions B: Process Metallurgy and Materials Processing Science, vol. 52, p. 1891-1914, jun. 2021, doi: 10.1007/s11663-021-02159-w. View Article
[24] A. Tazuddin, H. Aiyer, e A. Chatterjee, "Thermodynamic simulation in evaluating the role of minor oxides and mineralizers in Portland cement clinker phase formation", SN Applied Sciences, vol. 2, out. 2020, doi: 10.1007/s42452-020-03548-7. View Article
[25] P. Hewlett e M. Liska, Lea's chemistry of cement and concrete, 5o ed. Oxford: Butterworth-Heinemann (Elsevier), 2017. doi: 10.1016/C2013-0-19325-7. View Article
[26] I. H. Jung e M. A. Van Ende, "Computational thermodynamic calculations: FactSage from CALPHAD thermodynamic database to virtual process simulation", Metallurgical and Materials Transactions B: Process Metallurgy and Materials Processing Science, vol. 51, no 5, p. 1851-1874, out. 2020, doi: 10.1007/s11663-020-01908-7. View Article
[27] T. Hertel, A. Van den Bulck, S. Onisei, P. P. Sivakumar, e Y. Pontikes, "Boosting the use of bauxite residue (red mud) in cement - Production of an Fe-rich calciumsulfoaluminate-ferrite clinker and characterisation of the hydration", Cement and Concrete Research, vol. 145, jul. 2021, doi: 10.1016/j.cemconres.2021.106463. View Article
[28] D. Thompson e B. B. Argent, "Modelling trace and alkali mobilisation in the rotary cement kiln", Transactions of the Institutions of Mining and Metallurgy, Section C: Mineral Processing and Extractive Metallurgy, vol. 116, no 2, p. 115-122, jun. 2007, doi: 10.1179/174328507X163805. View Article
[29] K. Prasad, C. Srishilan, A. K. Shukla, e M. Kaza, "Thermodynamic assessment and experimental validation of clinker formation from blast furnace slag through lime addition", Ceramics International, vol. 44, no 16, p. 19434-19441, nov. 2018, doi: 10.1016/j.ceramint.2018.07.180. View Article
[30] D. A. Montoya, N. Pistofidis, G. Giannakopoulos, R. I. Iacobescu, M. S. Katsiotis, e Y. Pontikes, "Revisiting the iron-rich 'ordinary Portland cement' towards valorisation of wastes: study of Fe-to-Al ratio on the clinker production and the hydration reaction", Materials and Structures, vol. 54, no 30, fev. 2021, doi: 10.1617/s11527-020-01601-w. View Article
[31] X. Huang, S. Hu, F. Wang, L. Yang, M. Rao, Y. Mu, and C. Wang, "The effect of supplementary cementitious materials on the permeability of chloride in steam cured high-ferrite Portland cement concrete", Construction and Building Materials, vol. 197, p. 99-106, fev. 2019, doi: 10.1016/j.conbuildmat.2018.11.107. View Article
[32] S. A. Hayward, F. D. Morrison, S. A. T. Redfern, E. K. H. Salje, J. F. Scott, K. S. Knight, S. Tarantino, A. M. Glazer, V. Shuvaeva, P. Daniel, M. Zhang, and M. A. Carpenter, "Transformation processes in LaAlO3: Neutron diffraction, dielectric, thermal, optical, and Raman studies", Physical Review B: Condensed matter and materials physics, vol. 72, ago. 2005, doi: 10.1103/PhysRevB.72.054110. View Article
[33] M. Rizwan, S. Gul, T. Iqbal, U. Mushtaq, M. H. Farooq, M. Farman, R. Bibi, and M. Ijaz, "A review on perovskite lanthanum aluminate (LaAlO3), its properties and applications", Materials Research Express, vol. 6, no 11, set. 2019, doi: 10.1088/2053-1591/ab4629. View Article
[34] V. Shrivastava e R. Nagarajan, "Iron substitution in PrAlO3 perovskite leading to structural transformation and multiferroicity", Ceramics International, vol. 47, no 16, p. 22957-22964, ago. 2021, doi: 10.1016/j.ceramint.2021.05.009. View Article
[35] M. Harilal, V. M. Nair, P. R. S. Wariar, K. P. Padmasree, M. M. Yusoff, e R. Jose, "Electrical and optical properties of NdAlO3 synthesized by an optimized combustion process", Materials Characterization, vol. 90, p. 7-12, 2014, doi: 10.1016/j.matchar.2014.01.011. View Article
[36] G. R. Remya, S. Solomon, J. K. Thomas, e A. John, "Optical and dielectric properties of nano GdAlO3", em Materials Today: Proceedings, Elsevier Ltd, 2015, p. 1012-1016. doi: 10.1016/j.matpr.2015.06.027. View Article
[37] M. Shimada, H. Yamane, H. Takizawa, e T. Endo, "Phase transformation of Gd4Al2O9 at high temperature", Key Engineering Materials, vol. 132-136, p. 647-650, abr. 1997, doi: 10.4028/www.scientific.net/kem.132-136.647. View Article
[38] M. Shimada, T. Sakamoto, e H. Yamane, "Preparation and high temperature strength of Gd4Al2O9/MgO composites", Ceramic Materials and Components for Engines, p. 469-470, 2001, doi: 10.1002/9783527612765.ch79. View Article
[39] X. Zheng, J. Qi, Y. Zheng, e C. Liu, "Synthesis and characterization of CeAlO3 via solid state method", Journal of Solid State Chemistry, vol. 312, ago. 2022, doi: 10.1016/j.jssc.2022.123220. View Article
[40] F. Czerwinski, "Cerium in aluminum alloys", Journal of Materials Science, vol. 55, no 1, p. 24-72, jan. 2020, doi: 10.1007/s10853-019-03892-z. View Article
[41] D. Weiss, "Improved high-temperature aluminum alloys containing cerium", Journal of Materials Engineering and Performance, vol. 28, no 4, p. 1903-1908, abr. 2019, doi: 10.1007/s11665-019-3884-2. View Article
[41] D. Weiss, "Improved high-temperature aluminum alloys containing cerium", Journal of Materials Engineering and Performance, vol. 28, no 4, p. 1903-1908, abr. 2019, doi: 10.1007/s11665-019-3884-2. View Article